Cement
Found 15 results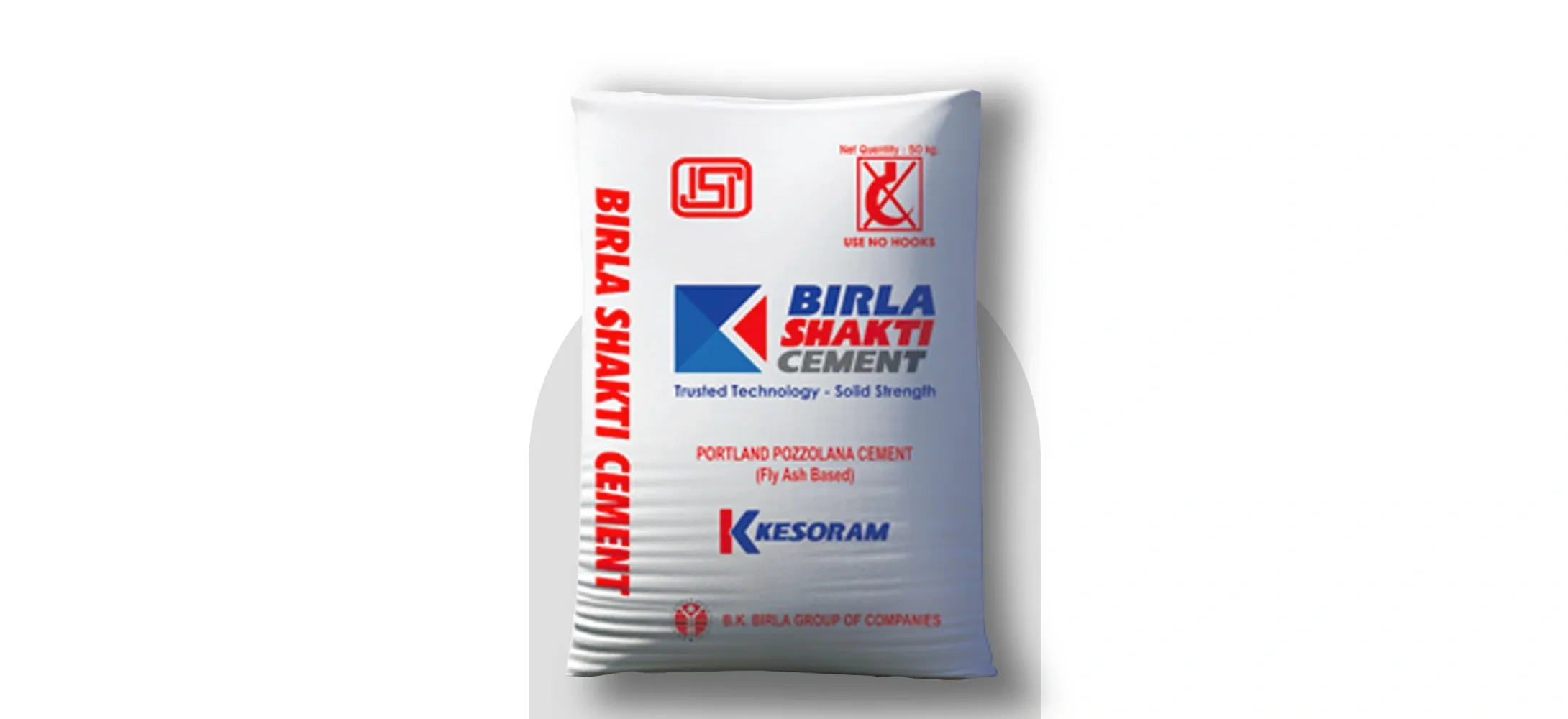
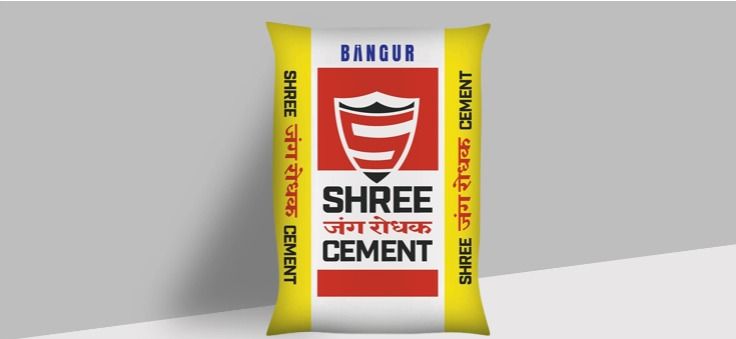
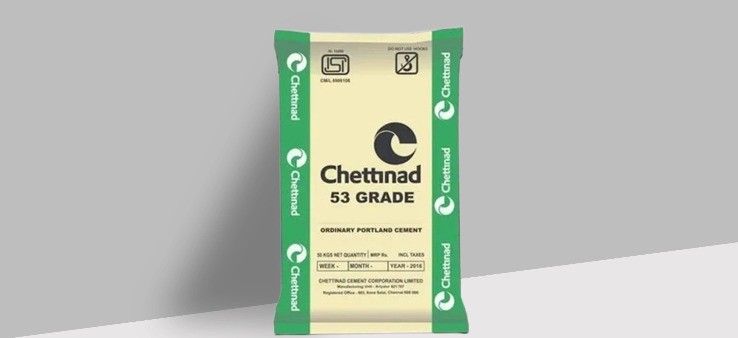
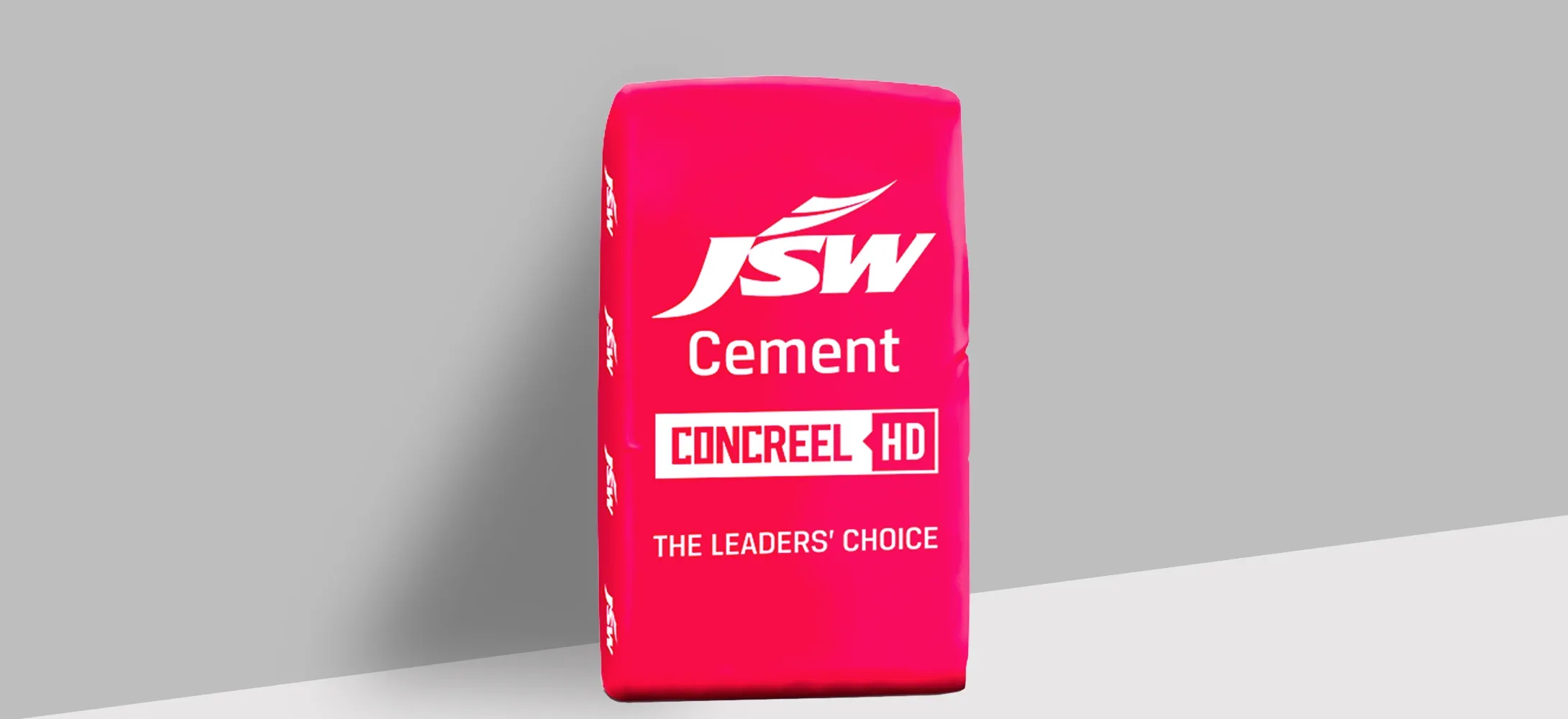
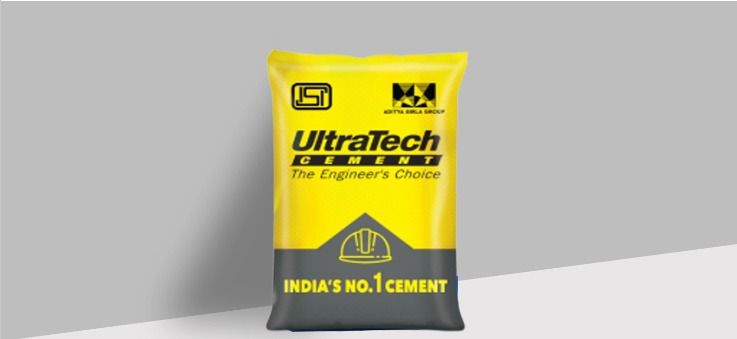
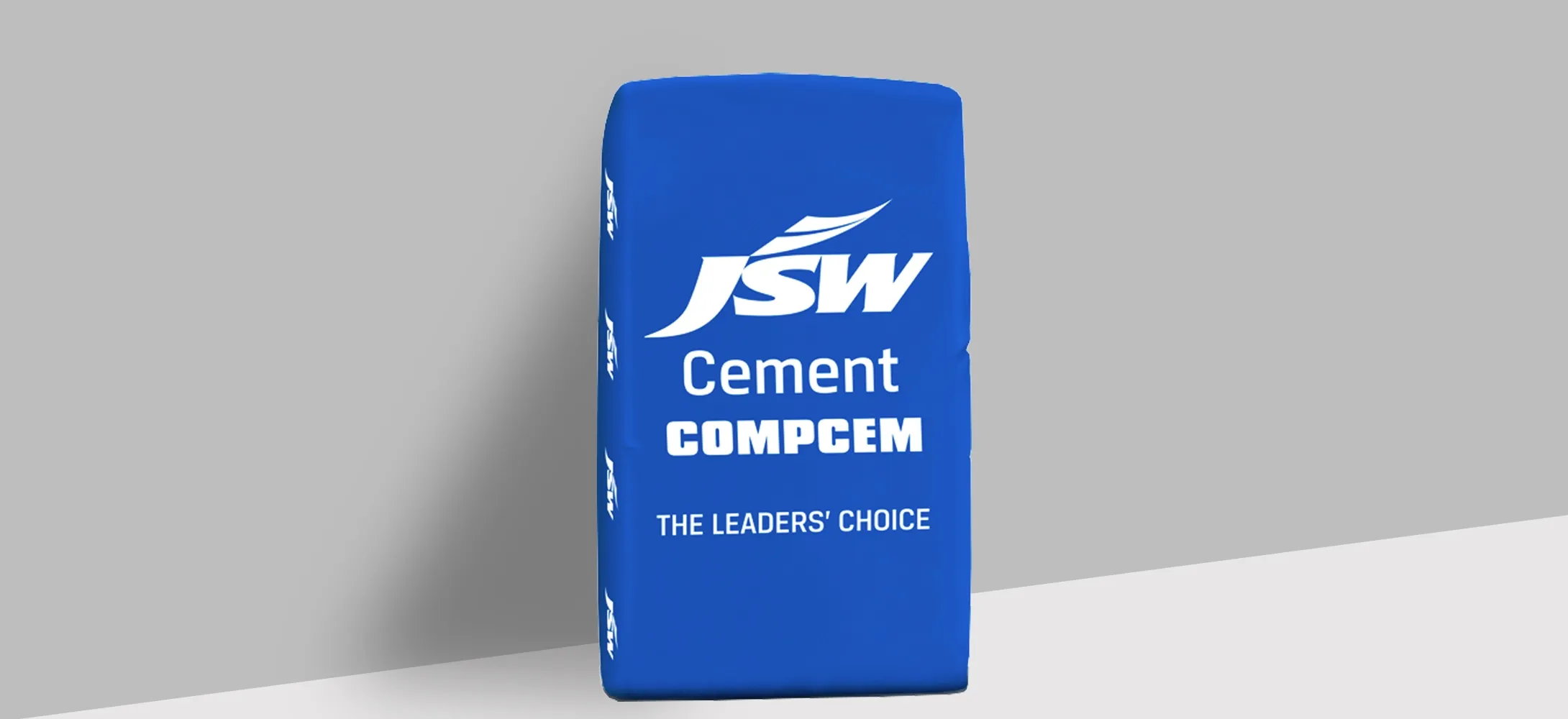
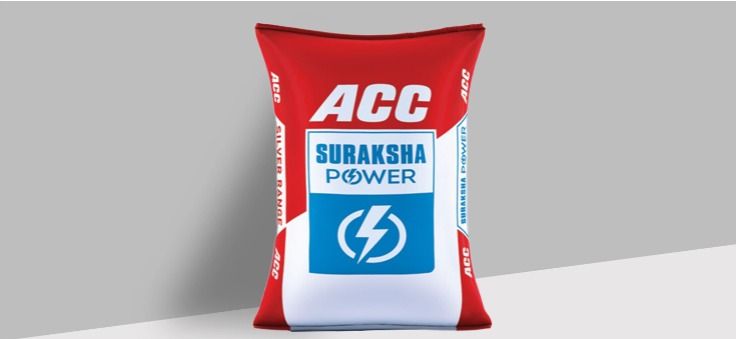
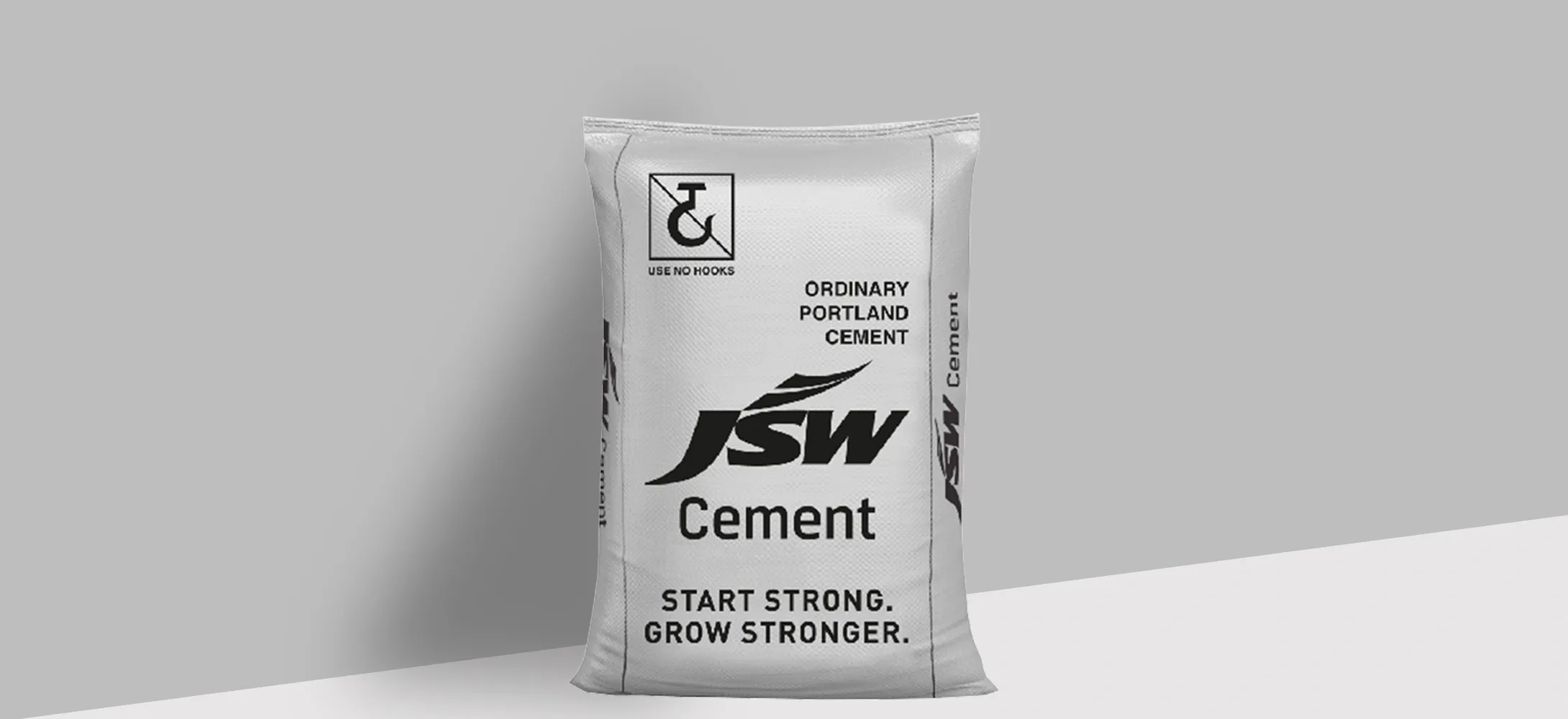
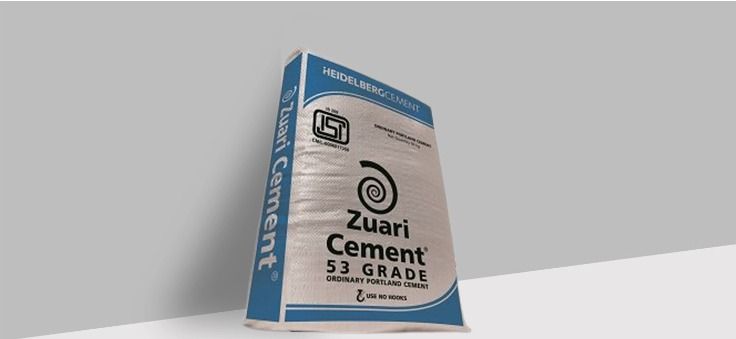
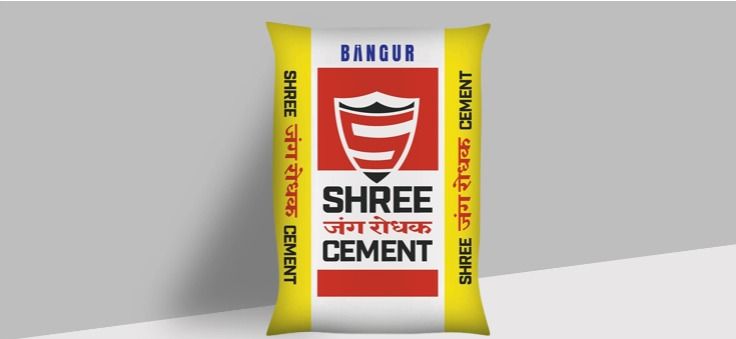
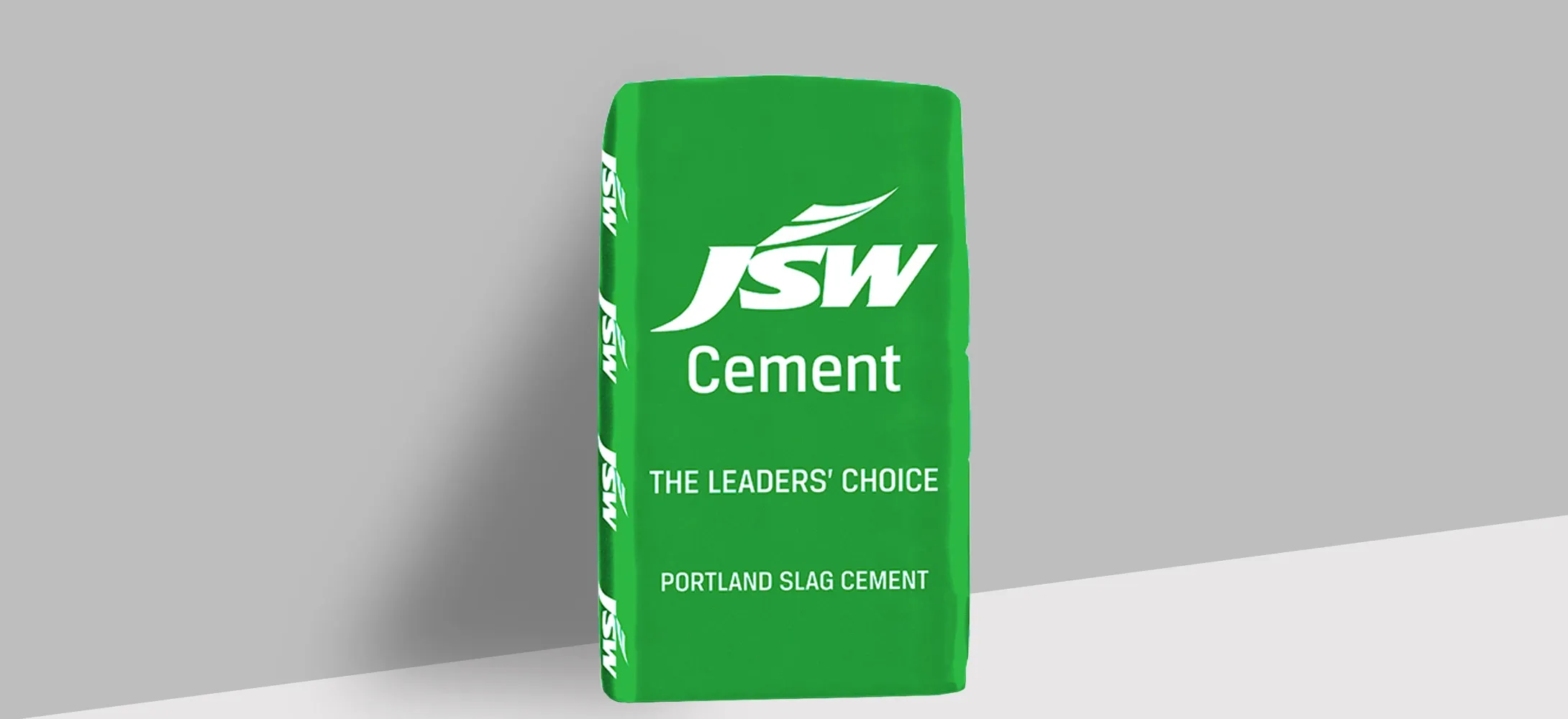
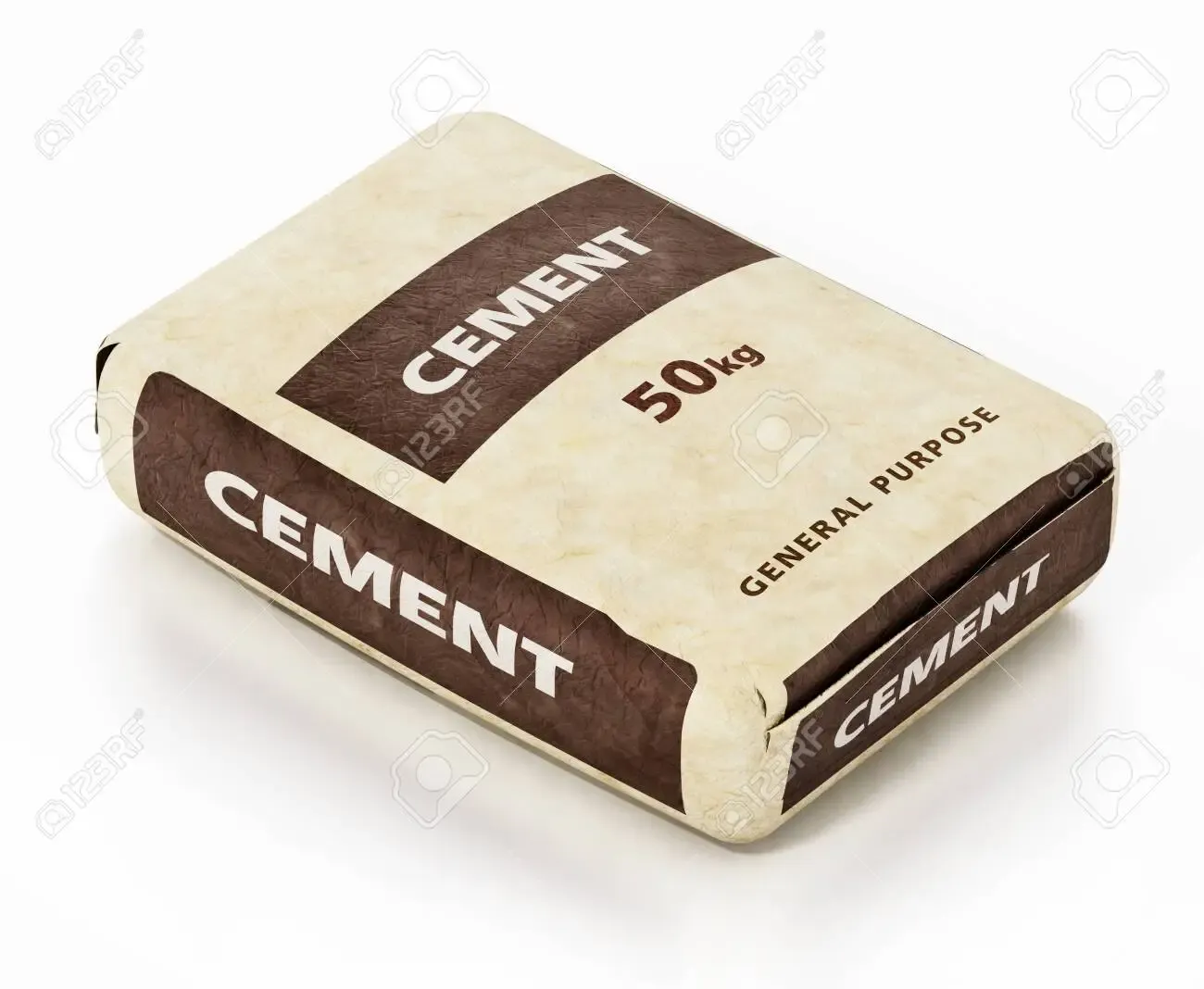
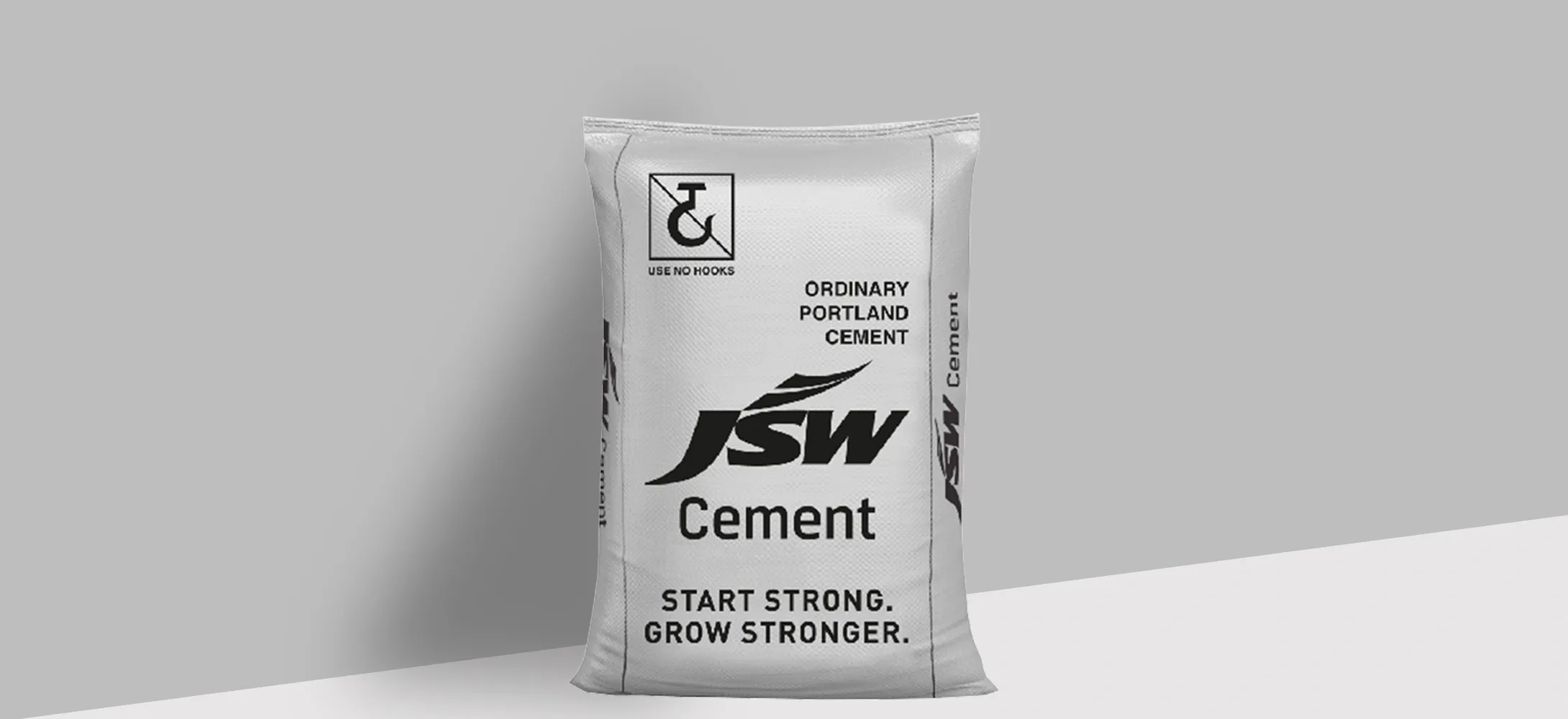

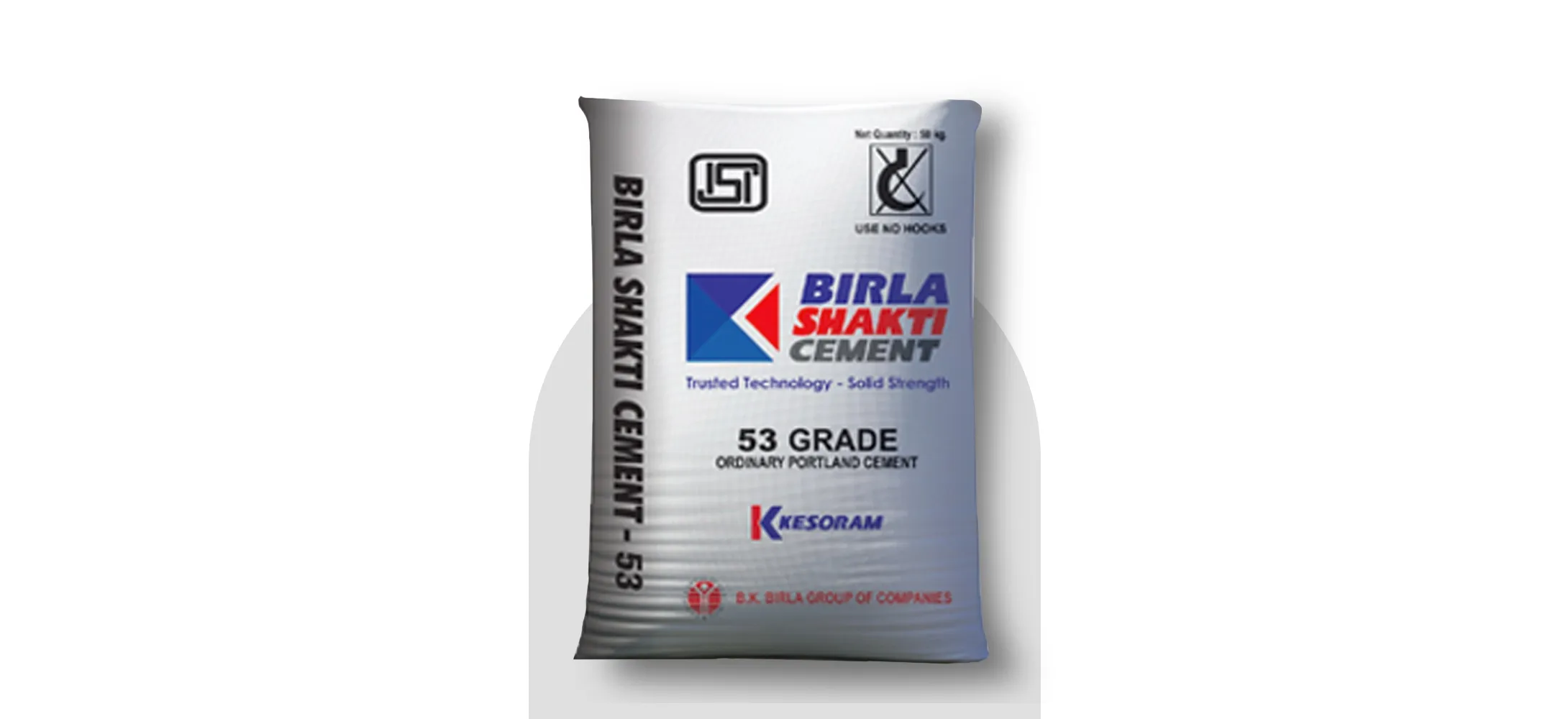
CEMENT
Cement is a cornerstone of India's infrastructure development, playing a pivotal role in building the nation’s urban and industrial landscape. As the world's second-largest cement producer, India boasts an installed capacity of approximately 500 million tonnes per annum, a testament to the sector's critical importance.
The industry's growth is fuelled by rapid urbanization and transformative government initiatives such as the Smart Cities Mission, Housing for All, and the development of industrial corridors. These programs aim to address the surging demand for urban housing and modern infrastructure, paving the way for India's transition into a global economic powerhouse. Significant investments in highways, railways, metro projects, and industrial parks further cement the industry's position as a key driver of the nation's growth trajectory. Choosing the right type of cement is vital for ensuring the durability and strength of structures, whether it’s a residential home, a high-rise building, or a large-scale infrastructure project.
Below, we delve into the various types of cement available in the market and their specific applications, offering insights to guide informed decisions for diverse construction needs.
Ordinary Portland Cement (OPC)
1. Raw material preparation The primary raw materials for OPC are limestone, clay, and gypsum. These materials are extracted from quarries and processed as follows:
- Limestone: the primary source of calcium oxide (CaO) in the raw mix, accounts for 60-65% of the mix. This finely ground raw mix will be fed into the kiln to produce clinker, which will then be ground to make cement.
- Clay/shale: provides silica (SiO₂), alumina (Al₂O₃), and iron oxide (Fe₂O₃), constituting 30–35% of the raw mix.
- Gypsum: added to control the setting time of the cement, typically 3–5% of the clinker weight.
Quantitative breakdown:
- Limestone: ~1400 kg per tonne of clinker
- Clay/shale: ~400-500 kg per tonne of clinker
- Gypsum: ~50 kg per tonne of cement
2. Proportioning and grinding The raw materials are proportioned based on the desired chemical composition and ground into a fine powder called raw meal. The raw meal is ground to a fineness of 90 microns. The typical composition in the raw meal:
- Calcium Oxide (CaO): 60–65%
- Silicon Dioxide (SiO₂): 20–25%
- Aluminium Oxide (Al₂O₃): 4–6%
- Iron Oxide (Fe₂O₃): 2–3%
3. Preheating and calcination
The ground raw meal is preheated (up to 900o Celsius) in a preheater tower using the hot gases from the kiln (a thermally insulated chamber, such as an oven, producing temperatures high enough to complete hardening, drying, or chemical processes). It then enters the kiln, where the temperature reaches up to 1450o Celsius. This stage involves several reactions, primarily calcination, which is the decomposition of calcium carbonate (CaCO₃) into calcium oxide (CaO) and carbon dioxide (CO₂).
4. Clinker formation
In the kiln, the raw meal undergoes various chemical reactions, leading to the formation of clinker, which is small, dark grey nodules. The critical compounds formed in the clinker are:
- Tricalcium silicate (C₃S or Alite): 50–70%
- Dicalcium silicate (C₂S or Belite): 15–30%
- Tricalcium aluminate (C₃A): 5–10%
- Tetracalcium aluminoferrite (C₄AF): 5-15%
Clinker composition:
- Alite (C₃S): ~65%
- Belite (C₂S): ~15%
- Aluminate (C₃A): ~10%
- Ferrite (C₄AF): ~8%
5. Cooling
The clinker is rapidly cooled using air to preserve the compounds' reactivity. Cooling is essential to maintain clinker quality and minimise energy consumption.
6. Grinding
The cooled 95% clinker is ground with 3-5% gypsum to form OPC. The fineness of grinding influences the cement's setting time and strength. The typical Blaine fineness for OPC is around 3000-3500 cm²/g.
Portland Slag Cement (PSC)
1. Raw material preparation
The primary raw materials for PSC are like those used in OPC, with the addition of Ground Granulated Blast-furnace Slag (GGBFS). These materials are extracted and processed as follows:
- Limestone: the primary source of calcium oxide (CaO).
- Clay/shale: provides silica (SiO₂), alumina (Al₂O₃), and iron oxide (Fe₂O₃).
- Gypsum: added to control the setting time of the cement.
- GGBFS: a by-product from the blast-furnaces used to make iron. It is rich in silica and alumina.
Quantitative breakdown:
- Limestone and clay/shale: Similar quantities to those used in OPC.
- GGBFS: typically 25-70% of the final cement mixture.
- Gypsum: ~5% of the final cement mixture.
2. Proportioning and grinding
The raw materials are combined in the right proportions to get the desired chemical composition. To make PSC, the OPC clinker, GGBFS, and gypsum are ground together. The cement's performance is greatly affected by how finely it's ground. For PSC, the mixture is ground to a Blaine fineness of about 4000-4500 cm²/g, which is usually finer than OPC.
3. Preheating and calcination
Heat the raw meal in a preheater tower using hot gases from the kiln. The preheated meal enters the kiln, reaching up to 1450o Celsius. During this process, calcium carbonate (CaCO₃) breaks down into calcium oxide (CaO) and carbon dioxide (CO₂).
4. Clinker formation
In the kiln, the raw meal undergoes chemical reactions to form clinker. It consists of tricalcium silicate (C₃S or Alite) at 50–70%, dicalcium silicate (C₂S) at 15–30%, tricalcium aluminate (C₃A) at 5–10%, and tetracalcium aluminoferrite (C₄AF).
5. Cooling
The clinker is rapidly cooled to preserve the compounds' reactivity. Rapid cooling helps to maintain clinker quality and reduce energy consumption.
6. Grinding
The cooled clinker is then mixed with GGBFS and gypsum and ground together to form PSC. The grinding process is critical as it influences the cement's final properties, such as setting time and strength.
Portland Pozzolana Cement (PPC)
1. Raw material preparation
PPC contains the same base materials as Ordinary Portland Cement (OPC), such as limestone, clay or shale, and gypsum. Additionally, it incorporates GGBFS along with fly ash, volcanic ash, calcined clay, or silica fume. Quantitative breakdown:
- Limestone and clay/shale: similar quantities to those used in OPC
- GGBFS: typically 15-35% of the final cement mixture
- Gypsum: ~5% of the final cement mixture
- Pozzolanic materials: like fly ash, volcanic ash, calcined clay, or silica fume are added to enhance the cement's long-term strength, durability, and resistance to chemical attacks. These materials typically constitute 15-35% of the final mixture
2. Proportioning and grinding
The raw materials are proportioned based on the desired chemical composition. The OPC clinker, pozzolanic materials, and gypsum are ground together to produce PPC. The fineness of grinding is crucial for the cement's performance. The mixture is ground to a Blaine fineness of around 3000-4000 cm²/g for PPC, which ensures optimal reactivity and strength development.
3. Preheating and calcination
For the OPC clinker, the raw meal is preheated and calcined similarly to OPC production:
- The raw meal is preheated in a preheater tower
- It then enters the kiln, where temperatures reach up to 1450o Celsius
- Calcination occurs, decomposing calcium carbonate (CaCO₃) into calcium oxide (CaO) and carbon dioxide (CO₂)
4. Clinker formation
In the kiln, the raw meal undergoes chemical reactions to form clinker. It consists of tricalcium silicate (C₃S or Alite) at 50–70%, dicalcium silicate (C₂S) at 15–30%, tricalcium aluminate (C₃A) at 5–10%, and tetracalcium aluminoferrite (C₄AF) at 5–15%.
5. Cooling and grinding
The clinker is rapidly cooled to preserve the compounds' reactivity. The cooled clinker is then mixed with pozzolanic materials and gypsum and ground together to form PPC. Composite Cement
- Raw material preparation: raw materials, including 65-75% clinker and Supplementary Cementitious Materials (SCMs), are proportioned based on the desired cement properties.
- Grinding: the raw materials are ground together to form a fine powder, ensuring a homogeneous mixture. The fineness of the grinding affects the cement's hydration and strength development.
- Blending: SCMs are blended with the ground clinker to achieve the desired composition. The blending process can occur in the mill or in separate mixing facilities.
- Packing and distribution: the final product is packed in bags or bulk and distributed to construction sites.
Grades of cement:
Cement Type | Grade | Strength (MPa) | Additional Details |
---|---|---|---|
Ordinary Portland Cement (OPC) | 33 Grade | 33 MPa after 28 days | - |
Ordinary Portland Cement (OPC) | 43 Grade | 43 MPa after 28 days | Releases medium heat of hydration. Used in M-30 grade concrete, which has a minimum strength of 30 MPa. M stands for Mix (proportions of cement, aggregate, and water). |
Ordinary Portland Cement (OPC) | 53 Grade | 53 MPa after 28 days | Releases higher heat of hydration. Suitable for projects requiring higher strength and quality assurance concrete. |
Portland Pozzolana Cement (PPC) | - | Comparable to OPC 33 and 43 | |
Portland Slag Cement (PSC) | - | Comparable to OPC 33 and 43 |
Cement Applications
Foundations and structural framework:
Cement is vital for building foundations and structural frameworks. It provides the necessary strength and durability to support the entire structure. High-strength cements like 53-grade OPC are often used in foundations to ensure stability, especially in high-rise buildings and bridges.
Masonry and plastering:
Cement binds bricks, stones, and blocks together in masonry work, forming walls and other structural elements. 43-grade OPC or PPC are commonly used due to their adequate strength and workability. These cements also create a smooth, even surface in plastering, enhancing the aesthetics and protective qualities of walls and ceilings.
Concrete for flooring and pavements:
Cement is essential for producing concrete used in flooring and pavements. The mix must withstand heavy traffic and environmental stress. 43-grade OPC is ideal due to its balance of strength and workability. Rapid hardening cement may be used for quick projects like road repairs, where early strength gain allows faster reopening.
Marine and hydraulic structures:
Marine and hydraulic structures, such as dams and docks, require cement that withstands harsh conditions. Portland Slag Cement (PSC) and Portland Pozzolana Cement (PPC) are perfect due to their resistance to sulphates and chlorides. These cements ensure long-term durability and strength in aggressive environments.
Decorative and architectural applications:
White Cement plays a significant role in decorative and architectural applications. Due to its smooth and attractive finish, white cement is used in precast facades, sculptures, and ornamental flooring. It allows architects to create visually appealing structures without compromising strength.
Cold weather construction:
Construction in cold climates faces challenges due to the slow curing of concrete. High alumina cement is ideal as it achieves high early strength, even in low temperatures. This property ensures projects can proceed efficiently without delays.
Industrial and chemical plants:
Cement used in industrial and chemical plants must resist chemical attacks and extreme conditions. Sulphate-resisting cement and high-alumina cement are commonly used. Sulphate-resisting cement is beneficial in areas with high sulphate content, while high-alumina cement offers superior resistance to chemical corrosion and high temperatures.
FAQs
Q: What is the difference between OPC vs PPC cement?
A: OPC has a fast-setting, high early strength, making it ideal for projects needing quick strength, such as roads and bridges.
PPC has a slower setting and better long-term strength and durability. It is suitable for mass concreting and structures exposed to harsh environments. The use of fly ash makes it more eco-friendly.
Q: How is cement made?
A: Cement is made by heating limestone, clay, and other materials in a kiln to form a clinker, which is then ground into a fine powder and mixed with gypsum.
Q: What is the difference between cement and concrete?
A: Cement is an ingredient in concrete. Concrete is a mixture of cement, water, sand, and aggregates used for construction.
Q: How should cement be stored?
A: Cement should be stored in a dry, moisture-free environment to prevent it from hardening. It’s best to keep it in its original packaging or sealed containers.
Q: What affects the setting time of cement?
A: Factors like temperature, humidity, water-cement ratio, and the type of cement can affect how quickly or slowly cement sets.
Q: How do you test cement quality?
A: Common tests include fineness, consistency, setting time, strength, and soundness tests to ensure the cement meets the required standards for construction use.
Q: What are the environmental benefits of PPC and PSC?
A: PPC and PSC are eco-friendly as they use industrial by-products, reducing waste and raw material demand. They have a lower carbon footprint, conserve energy, and result in more durable concrete, reducing the need for frequent repairs.
Buy online
Mild SteelStainless SteelStructural SteelTMTCementJSW One MSME
About usBlogsSitemapJSW One TMTPolicy
Terms & conditionsPrivacy policyReturn policyBanking partner