Industrial sheds are vital infrastructure for MSMEs, providing essential space for manufacturing processes, storage, and more. These sheds' structural integrity and longevity depend heavily on the materials used—particularly steel. Steel is the preferred material for constructing robust industrial sheds with high tensile strength, flexibility, and durability. This technical guide explores the key considerations and best practices for using steel in industrial shed construction to maximise performance and durability.
1. Material selection: choosing the right steel grade
Selecting the appropriate steel grade is fundamental to the performance of your industrial shed. The choice of steel should be based on the structural requirements, environmental conditions, and intended lifespan of the shed.
Hot-rolled steel (HR steel): this steel is recommended for primary structural components such as columns, beams, and trusses. HR steel, typically in grades E250 and E350, provides excellent load-bearing capacity and can withstand dynamic stresses and heavy loads.
Cold-rolled steel (CR steel): suitable for secondary structural elements, including purlins and girts, where dimensional accuracy and surface finish are critical. CR steel grades such as CR2 are preferred for applications requiring tight tolerances.
Galvanised steel (GP steel): for components exposed to external environments, GP steel with zinc coating offers superior corrosion resistance, ensuring the longevity of the shed's exterior elements. This steel is particularly effective in coastal or high-humidity environments.
Galvalume steel: a blend of aluminium and zinc coating, galvalume provides enhanced corrosion resistance compared to traditional galvanised steel, making it ideal for roofing and cladding applications.
Tips on using steel in the design and construction of durable industrial sheds
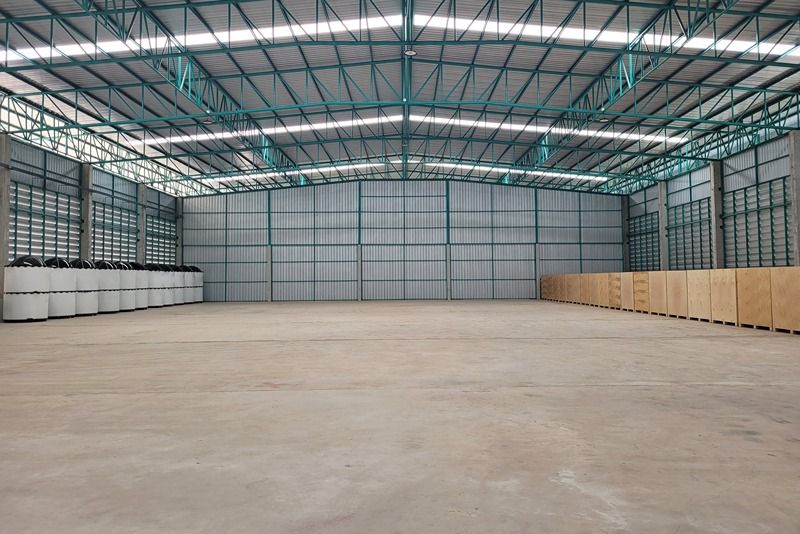
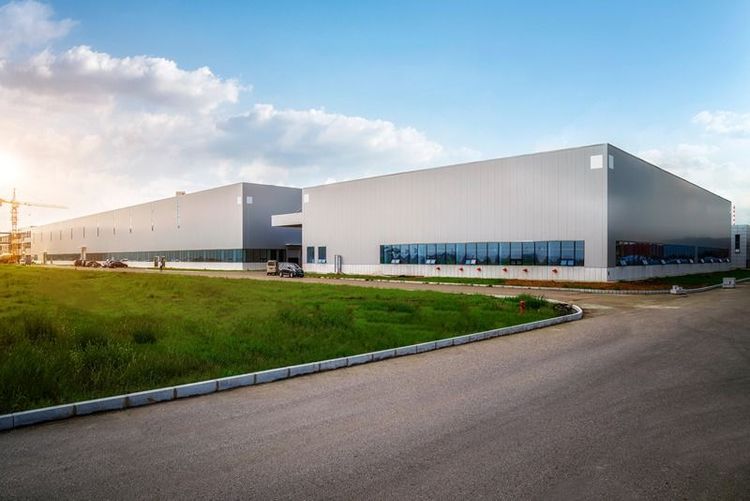
2. Structural design: engineering for strength and stability
The structural design of an industrial shed must consider factors such as load-bearing capacity, wind and seismic forces, and future scalability. Adhering to local building codes and international standards is critical for ensuring structural safety.
Load-bearing capacity:
Dead loads: calculate the dead load based on the weight of the steel structure, roofing materials, and any permanent equipment or fixtures. HR steel grades E250 and E350 are commonly used for the primary load-bearing structure.
Live loads: consider dynamic loads, including equipment, inventory, and workforce activity. For heavy-duty applications, opt for higher-grade steels or reinforced structural members.
Wind load and seismic design:
Wind loads: use computational fluid dynamics (CFD) analysis to model wind forces on the shed. Design the structure to resist wind uplift and lateral forces, ensuring that connections and anchor points can transfer these forces to the foundation.
Seismic forces: in seismic zones, lateral force-resisting systems such as braced or moment-resisting frames are incorporated. Design steel connections to allow ductility and energy dissipation during seismic events.
Modular design for scalability:
Pre-engineered building systems (PEBs): consider PEBs for modular construction, allowing for easy expansion or reconfiguration. Modular components should be designed for easy assembly and disassembly, facilitating future modifications with minimal disruption.
3. Corrosion protection: enhancing the durability of steel structures
Corrosion is a major concern in steel structures, especially in industrial settings exposed to moisture, chemicals, or extreme weather. Implementing effective corrosion protection strategies is essential for extending the lifespan of the shed.
Protective coatings:
Galvanisation: apply hot-dip galvanisation (HDG) to structural steel members for robust protection against corrosion. The thickness of the zinc coating should be selected based on the expected exposure conditions (e.g., iso 1461 standard for HDG).
Epoxy and polyurethane coatings: for additional protection, especially in aggressive environments, apply epoxy or polyurethane coatings over galvanised steel. These coatings provide a secondary barrier against moisture and chemical exposure.
Cathodic protection:
Consider using cathodic protection systems in environments with severe corrosion risk (e.g., coastal or chemical plants). This technique uses sacrificial anodes or impressed current systems to protect steel components from corrosion.
Maintenance protocols:
Establish a maintenance schedule for regular inspection and re-application of protective coatings. Early detection and treatment of corrosion can prevent structural degradation and costly repairs.
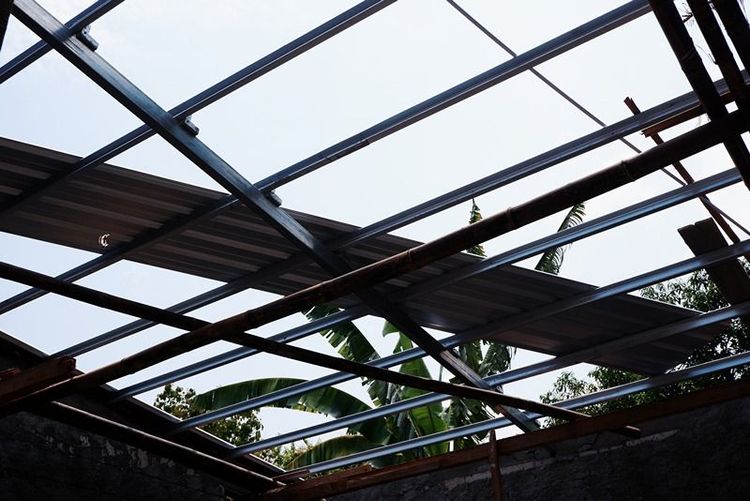
4. Thermal insulation and ventilation: maintaining environmental control
Thermal and environmental control within the shed is crucial for both operational efficiency and the preservation of stored goods. Appropriate insulation and ventilation systems are essential for maintaining optimal internal conditions.
Insulation materials:
Insulated metal panels (IMPS): for effective thermal insulation, use imps with a core of polyurethane or polyisocyanurate foam. These panels offer a high R-values, reducing heat transfer and maintaining a stable internal temperature.
Reflective insulation: for roofing, consider installing reflective insulation to minimise heat gain. This is particularly beneficial in hot climates, significantly reducing cooling loads.
Ventilation systems:
Natural ventilation: design the shed with strategically placed openings, such as ridge vents, louvred vents, and operable windows, to facilitate natural airflow and prevent heat buildup.
Mechanical ventilation: in cases where natural ventilation is insufficient, install mechanical ventilation systems, including exhaust fans and air circulators. Ensure that these systems are designed to provide adequate air changes per hour (ach) for the shed’s volume and use case.
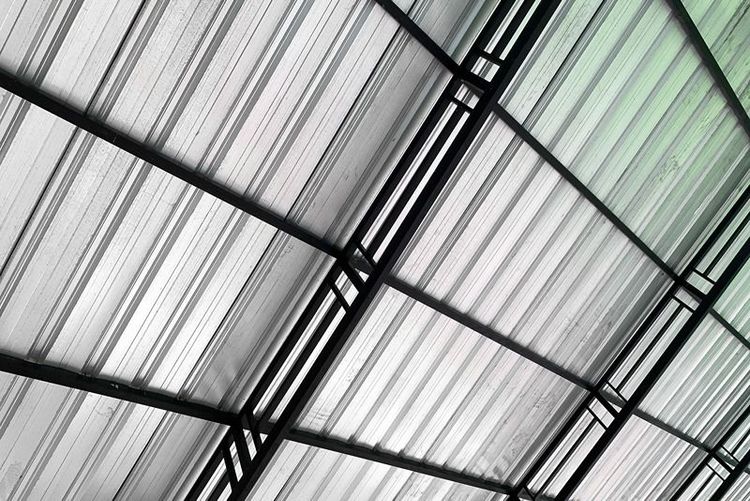
5. Prefabrication and modular construction: streamlining the build process
Prefabrication and modular construction methods offer numerous advantages, including reduced construction time, improved quality control, and lower labour costs. Leveraging these methods can enhance the efficiency of industrial shed construction.
Prefabricated steel components:
Precision manufacturing: prefabricated components are manufactured under controlled conditions, ensuring high precision and reducing on-site errors. Use computer-aided design (CAD) and computer-aided manufacturing (CAM) systems to optimise the design and production of steel components.
Assembly efficiency: prefabricated components are delivered to the site ready for assembly, significantly reducing construction time. Design connections for ease of assembly, using bolted or welded connections as appropriate.
Integrated building systems:
Structural systems: use integrated structural systems where the primary frame, roof, and wall panels are designed as a cohesive unit. This approach ensures compatibility and reduces the need for on-site modifications.
Mechanical, electrical, and plumbing (MEP) integration: where possible, pre-integrate MEP systems into the modular components. This reduces installation time and ensures these systems are properly coordinated with the structural elements.
Conclusion
Constructing a durable industrial shed requires meticulous planning, precise engineering, and a deep understanding of the materials and methods involved. By selecting the appropriate steel grades, designing for structural integrity, incorporating effective corrosion protection, and leveraging modular construction techniques, MSMEs can build sheds that meet current operational needs and provide the flexibility to adapt to future demands.
JSW One MSME offers a comprehensive range of high-quality steel products engineered for industrial applications. Our technical experts are available to assist you in selecting the right materials and solutions for your project. Explore our JSW One MSMEe-commerce platform offerings and partner with us to build a shed that stands the test of time and drives your business forward.
Buy online
Mild SteelStainless SteelStructural SteelTMTCementJSW One MSME
About usBlogsSitemapJSW One TMTPolicy
Terms & conditionsPrivacy policyReturn policyBanking partner