Pre-Engineered Building (PEB) systems and conventional buildings represent two distinct approaches to construction, each with its own advantages and limitations. With the rapid growth in India's infrastructure development, understanding these differences can help builders, engineers, and project managers make informed decisions that align with project requirements. Below, we explore the technical and practical differences between PEB systems and conventional buildings.
1. Design and engineering flexibility
PEB systems: these structures are designed and fabricated using pre-determined dimensions and specifications, optimised through specialised software. The components are engineered to work together cohesively, ensuring efficient load distribution and reducing the need for excess material. This approach allows for design adaptability within a modular framework, providing options for customisation while maintaining cost and time efficiency.
Pre-engineered steel building systems vs conventional buildings
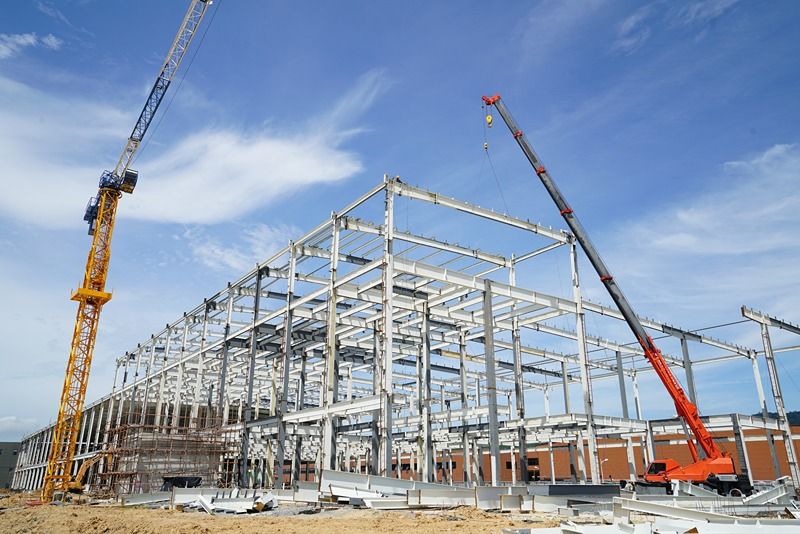
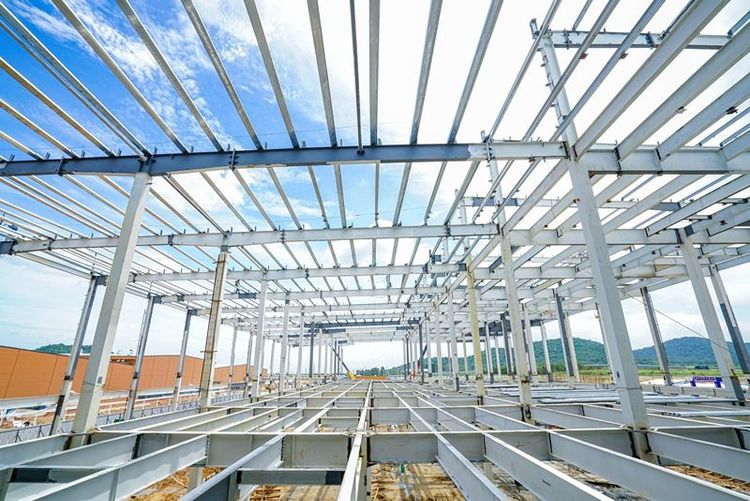
Conventional buildings: in traditional construction, every building is designed from scratch according to specific project requirements. This results in greater design flexibility but often requires more detailed engineering calculations and a longer design process. Customised architectural features and complex layouts can be incorporated more easily, often leading to increased costs and extended project timelines.
2. Construction time
PEB systems: one of the standout advantages of PEBs is their rapid assembly. Components are prefabricated in a factory and transported to the construction site for quick installation. This minimises on-site labour and significantly reduces construction timelines—often by 30-50% compared to conventional methods. The streamlined process means fewer delays due to weather or labour shortages, making PEBs ideal for projects with tight schedules.
Conventional buildings: these structures require on-site fabrication, including formwork, reinforcement, and concrete pouring. Construction often involves multiple trades and can be heavily affected by on-site conditions, leading to longer timelines. The process typically requires detailed coordination between different teams, which can contribute to potential delays.
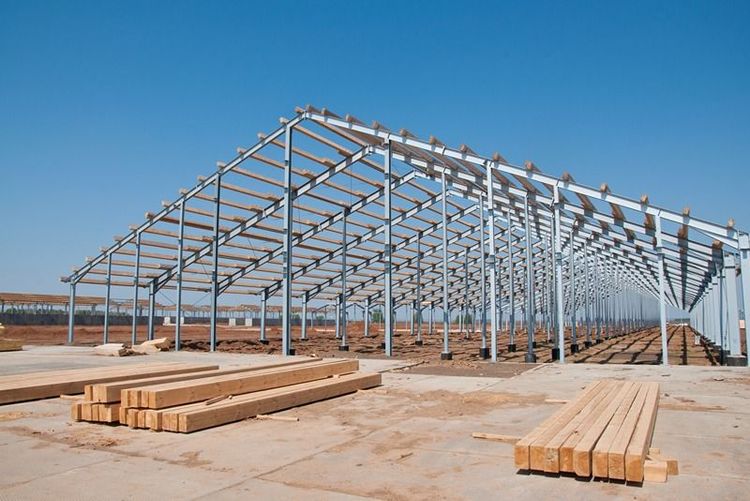
3. Material efficiency and structural weight
PEB systems: these systems use optimised steel sections, such as hot-rolled and cold-formed components, tailored for specific structural needs. Grades like IS 2062 E250 and E350 are often employed to achieve the required strength-to-weight ratio. The precise engineering of PEBs means less material is wasted, resulting in lighter structures that maintain high load-bearing capacities. This efficiency reduces the overall weight of the building, which in turn can lower foundation costs.
Conventional buildings: these often use heavier sections, such as reinforced concrete and conventional steel frames. While robust, these structures generally involve excess material due to less precise engineering, leading to higher overall building weight. The use of concrete, for example, adds significant mass, necessitating deeper and more reinforced foundations, which can increase costs.
4. Cost considerations
PEB systems: they typically offer a lower overall cost due to standardisation and efficient use of materials. Prefabrication helps maintain budget predictability by reducing waste and labour costs. The quicker construction timeline also contributes to cost savings, requiring fewer on-site resources.
Conventional buildings: they may initially appear less expensive due to more readily available materials like concrete and standard steel sections. However, the extended project duration and increased on-site labour can lead to higher overall costs. Additionally, custom designs often require more engineering and material, increasing expenses further.
5. Quality control and construction accuracy
PEB systems: components are manufactured in a controlled environment with stringent quality checks, ensuring high precision and adherence to design specifications. Factory production minimises defects and discrepancies that can arise during manual on-site fabrication. The assembly process is also straightforward, requiring fewer adjustments.
Conventional buildings: quality control is more variable as construction takes place on-site. Human error, inconsistent material supply, and environmental conditions can affect the final build quality. While site supervisors and engineers can monitor the process, achieving uniform quality can be more challenging than factory-controlled fabrication.
6. Structural durability and maintenance
PEB systems: modern steel grades used in PEBs, such as IS 2062 E350, provide excellent resistance to environmental factors, making these buildings durable over long periods. The structures are designed with built-in tolerances for expansion and contraction, accommodating climate variations across India. Maintenance is typically lower, as steel structures resist cracking and termite damage.
Conventional buildings: while reinforced concrete can provide substantial durability and fire resistance, it may be prone to issues like cracking, spalling, and corrosion of the steel reinforcement, especially in high-humidity environments. Maintenance needs for concrete buildings can be higher over time, particularly for older structures or those exposed to aggressive conditions.
7. Sustainability and recyclability
PEB systems: steel is inherently recyclable, contributing to the sustainability of PEBs. Recyclable steel components align with modern green building standards and support eco-friendly construction practices. Additionally, the precision of prefabrication minimises waste, further enhancing sustainability.
Conventional buildings: while concrete can be partially recycled, the process is more complex and energy-intensive than steel recycling. Additionally, conventional construction often results in more material waste during the build phase, which can contribute to a higher environmental footprint.
Conclusion: choosing between PEB and conventional construction
Both PEB systems and conventional buildings have their place in construction, but the choice depends on project-specific requirements. PEBs excel in projects needing rapid completion, cost control, and material efficiency, making them ideal for industrial, commercial, and warehouse applications. Conventional buildings are more suitable for custom architectural designs and projects that prioritise material and load-bearing flexibility.
Buy online
Mild SteelStainless SteelStructural SteelTMTCementJSW One MSME
About usBlogsSitemapJSW One TMTPolicy
Terms & conditionsPrivacy policyReturn policyBanking partner