Welding stands as a critical process in construction, bringing together disparate pieces of metal into a cohesive structure. In recent years, Thermo-Mechanically Treated (TMT) steel has gained significant popularity in construction due to its superior strength and durability. However, welding a TMT steel bar comes with its set of challenges. In this blog, we will explore the intricacies of TMT steel welding, addressing common challenges and providing solutions to ensure successful welds in construction projects.
Understanding TMT
Steels for TMT bars are designed in such a way to provide weldability. Moreover, TMT bar undergoes a specialised manufacturing process involving controlled heating and rapid cooling to enhance its mechanical properties. This process results in a steel product with high strength, ductility, and weldability.
Properties that make TMT popular in construction
TMT's properties like high tensile strength and superior bendability make it suitable for a variety of structural applications. However, these very properties can pose challenges during the welding process.
TMT finds applications in a range of construction projects, from high-rise buildings to bridges. Understanding its applications is crucial for welders to tailor their techniques to the specific requirements of each project.
How to overcome welding challenges with TMT steel?
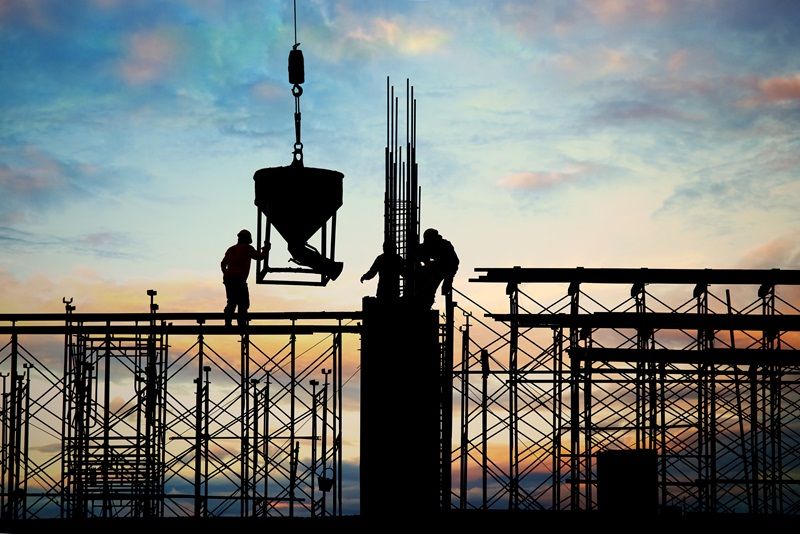
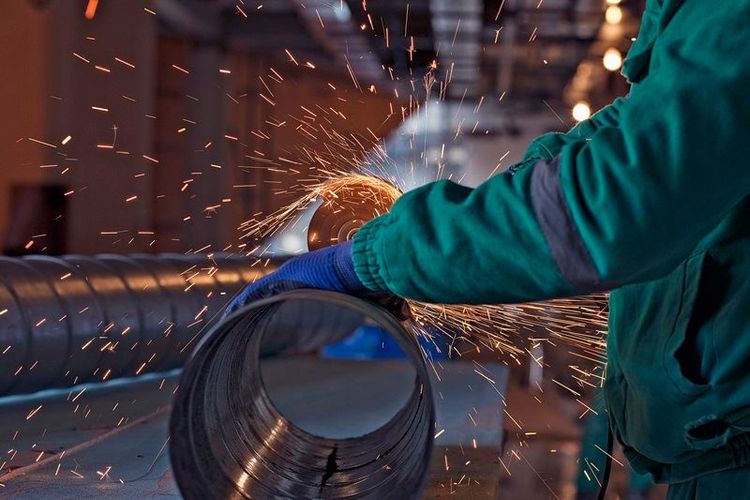
Challenges in welding TMT bar
High carbon content and its implications
TMT's high carbon content, while contributing to its strength, poses challenges during welding. High carbon content can lead to increased hardness and promote brittleness in the Heat-Affected Zone (HAZ) and may result in issues such as cracking.
Thermal treatment effects on weldability
The thermo-mechanical treatment process alters the microstructure of TMT rebar, affecting its weldability. Welders need to be aware of these changes and adjust their techniques accordingly to prevent issues like reduced ductility.
Potential for cracking and distortion
One of the primary challenges in welding a TMT steel bar is the potential for cracking and distortion. The rapid cooling during the manufacturing process can create internal stresses that may manifest as cracks during welding.
Pre-welding preparations
Proper storage and handling of TMT steel
Before welding, proper storage and handling of a TMT steel bar are essential. Exposure to moisture and contaminants can compromise the quality of the steel and lead to welding difficulties.
Understanding TMT grades
Different grades of TMT steel have varying compositions and properties. Understanding the specific grade being used is crucial for selecting the right welding techniques and consumables. Selection of grades based on the Carbon Equivalent (CE) values is essential to ensure better weldability of the TMT bars.
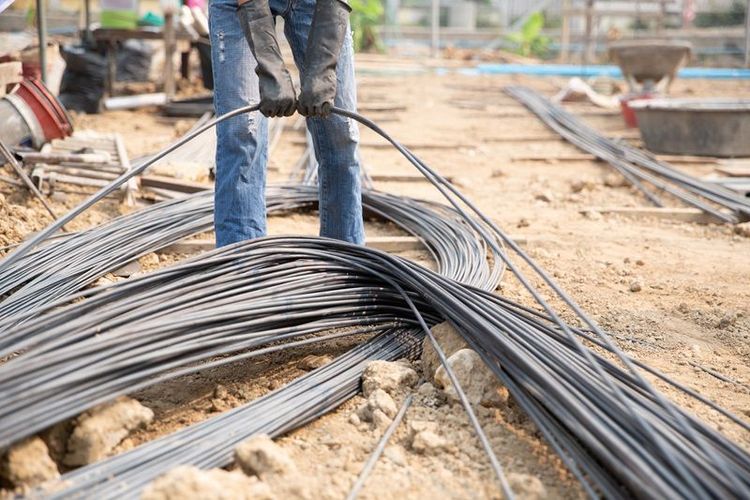
Surface cleaning and removal of contaminants
Cleanliness is paramount in TMT welding. Proper surface cleaning and removal of contaminants, such as rust and scale, ensure a clean welding environment and prevent defects in the weld.
Welding techniques for TMT steel bar
Choosing the right welding process
Selecting the appropriate welding process is critical for TMT. Common processes include Shielded Metal Arc Welding (SMAW), Gas Metal Arc Welding (GMAW), and Submerged Arc Welding (SAW). Each has its advantages and challenges, and the choice depends on factors such as material thickness and project requirements.
In SMAW, an electrode with a flux coating is used. The heat generated by an electric arc between the electrode and the workpiece melts both the electrode and the workpiece, creating a weld pool. The flux coating on the electrode forms a shielding gas, protecting the weld pool from atmospheric contamination.
GMAW utilises a wire electrode that is continuously fed from a spool. The welding machine releases a shielding gas, typically a mixture of argon and carbon dioxide, to protect the weld pool from atmospheric contaminants.
SAW is a method where the welding arc is hidden under a layer of granular flux. This layer shields the arc from air, keeping the weld clean.
Adjusting heat input and welding parameters
Controlling heat input is crucial when welding TMT steel. Excessive heat can lead to increased hardness and potential cracking. Welders must carefully adjust welding parameters, including voltage, current, and travel speed, to achieve optimal results.
Preheating and post-weld heat treatment considerations
Preheating the TMT before welding helps reduce the temperature differential between the weld and the surrounding material, minimising the risk of cracking. Post-weld heat treatment may also be necessary to relieve residual stresses and improve the overall weld quality.
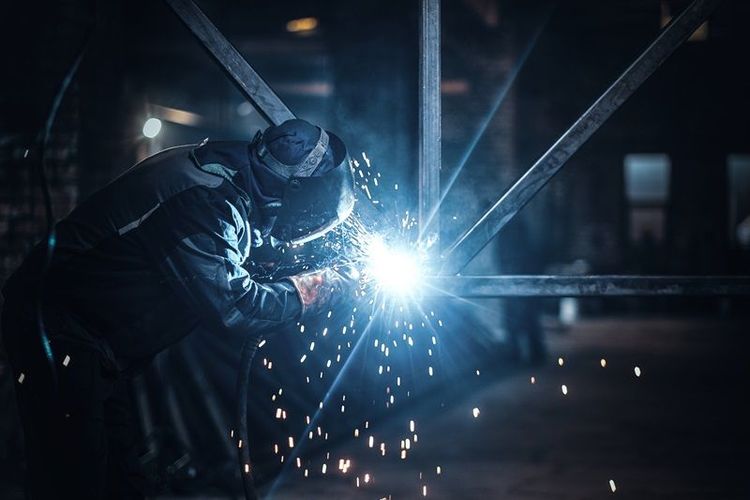
Selecting the right consumables
Choosing appropriate welding electrodes
The selection of welding electrodes is critical in TMT welding. Electrodes with proper flux composition can help control the cooling rate, reduce the risk of cracking, and ensure a sound weld.
Importance of fluxes in TMT welding
Fluxes play a vital role in shielding the weld from atmospheric contamination. They also contribute to the overall quality of the weld by controlling the arc characteristics and providing essential elements to the molten weld pool.
In processes like GMAW, the choice of shielding gases is crucial. The right combination of gases helps achieve proper penetration and reduces the likelihood of defects in the weld.
Quality control measures
Non-Destructive Testing (NDT) for welded joints
Implementing non-destructive testing methods, such as ultrasonic testing and magnetic particle testing, is essential for verifying the integrity of welded joints. These tests can detect internal defects without compromising the structure.
Visual inspection and dimensional checks
Regular visual inspections, including checks for weld bead appearance and uniformity, are essential. Dimensional checks ensure that the weld conforms to specified tolerances, preventing potential structural issues.
Ultrasonic testing and radiography for critical welds
For critical welds, particularly in load-bearing structures, ultrasonic testing and radiography provide in-depth insights into the internal soundness of the weld. These methods are crucial for ensuring the long-term structural integrity of the welded joints.
Post-welding treatment
Stress relieving techniques for TMT
Stress-relieving post-weld heat treatments can help mitigate residual stresses in the welded joints. This is particularly important in applications where dimensional stability and long-term durability are paramount.
Machining and finishing processes
Machining and finishing processes, such as grinding and polishing, contribute to the aesthetic and functional aspects of the weld. These processes also help eliminate potential stress concentration points and improve the overall appearance of the welded structure.
Corrosion protection measures
TMT rebar structures are often exposed to environmental elements that can lead to corrosion. Implementing effective corrosion protection measures, such as coatings or cathodic protection systems, ensures the longevity of the weld and the entire structure.
Best practices and tips
Maintaining detailed documentation of welding procedures is essential for consistency and quality control. Documented procedures serve as a reference for future projects and contribute to the standardisation of welding practices. The field of welding is dynamic, with new technologies and techniques emerging regularly. Providing continuous training for welding personnel ensures that they stay abreast of the latest developments and refine their skills accordingly.
Buy online
Mild SteelStainless SteelStructural SteelTMTCementJSW One MSME
About usBlogsSitemapJSW One TMTPolicy
Terms & conditionsPrivacy policyReturn policyBanking partner