Corrosion fatigue refers to the progressive degradation of material due to the combined effects of cyclic stress (fatigue) and corrosive environments. In the case of TMT bars, which are used in reinforced concrete structures, this phenomenon occurs when the bars are exposed to repetitive loading and environmental elements like moisture, salt, and chemicals, leading to premature failure. Unlike typical fatigue, where materials degrade in dry or inert environments, corrosion fatigue involves the influence of environmental factors like humidity or saltwater, which accelerate crack growth.
The repetitive loading causes micro-cracks in the bars, and when combined with exposure to corrosive agents, these cracks propagate more quickly, weakening the steel. Over time, this degradation reduces the load-bearing capacity of the bars, leading to the potential collapse of the structure if not properly managed.
Causes of corrosion fatigue in TMT bars
Several factors contribute to corrosion fatigue in TMT bars, especially in India's diverse climatic conditions:
Environmental exposure
The most common cause of corrosion fatigue is exposure to a corrosive environment. Structures near coastal regions are particularly vulnerable to high salt content in the air, which accelerates the corrosion of TMT bars. Additionally, areas with high humidity or industrial pollution are prone to creating corrosive environments, weakening the bars over time.
Corrosion fatigue in TMT bars: causes and prevention methods
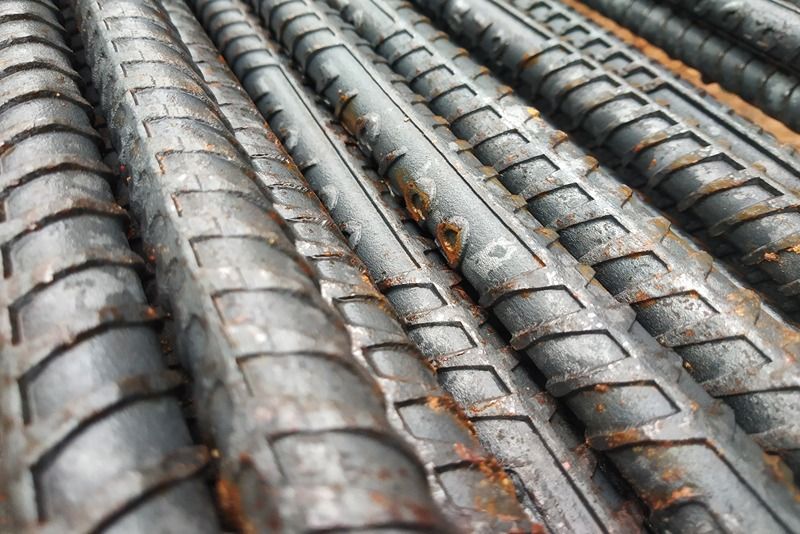
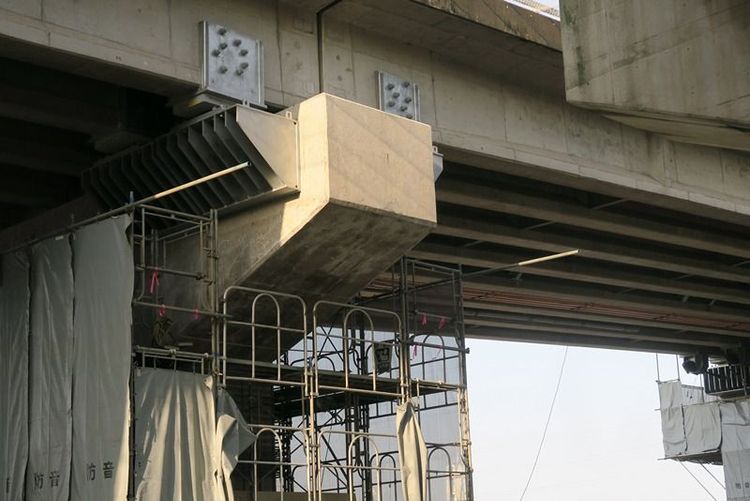
Moisture ingress
Moisture entering the concrete structure through cracks or poor-quality concrete mix can accelerate the corrosion process. Water and oxygen reaching the TMT bars initiate the rusting process, leading to the weakening of the steel’s protective oxide layer. Over time, the cyclic stress from load-bearing in the presence of this rust formation increases the risk of fatigue.
Cyclic loading
Structures that undergo repetitive loading cycles, such as bridges, highways, and industrial buildings, are more prone to fatigue. The combination of constant stress and corrosion accelerates crack growth in TMT bars, weakening the steel and reducing its ability to support the loads it was designed for.
Chloride attack
Chloride ions, which are abundant in coastal areas or regions where de-icing salts are used, penetrate concrete and initiate corrosion in TMT bars. Chlorides break down the passive oxide layer on steel, leading to accelerated corrosion and fatigue when combined with mechanical stress.
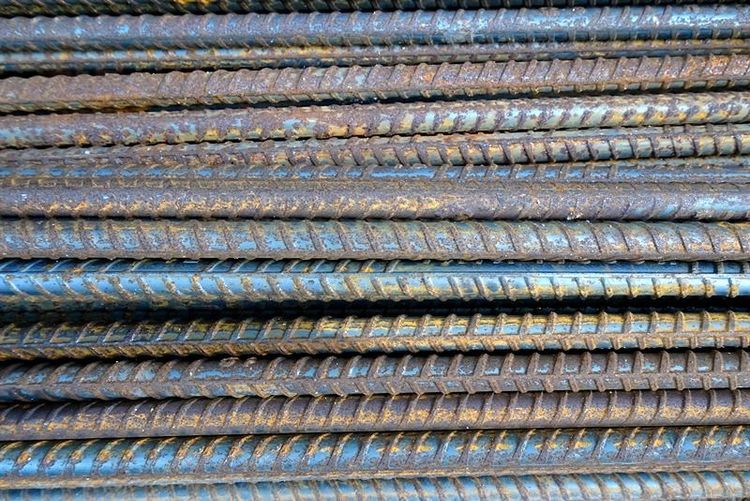
Poor concrete quality
The quality of the concrete mix used in construction significantly impacts the performance of TMT bars. Poor-quality concrete with high porosity allows more moisture and corrosive agents to penetrate, accelerating the corrosion process. Additionally, improper curing and placement techniques can leave gaps in the concrete, exposing TMT bars to the elements.
Micro-cracking during the manufacturing process
If TMT bars have pre-existing micro-cracks formed during the manufacturing or quenching process, these cracks can act as stress concentrators. When exposed to corrosive environments, these cracks expand under cyclic loading, leading to premature fatigue failure.
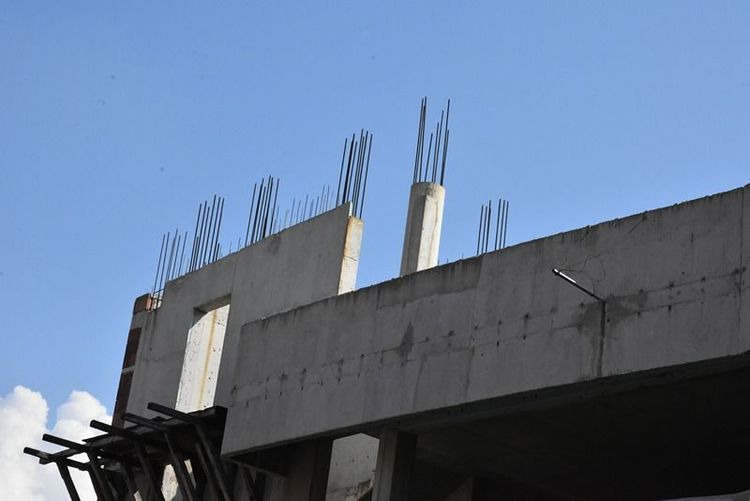
Prevention methods for corrosion fatigue
To prevent corrosion fatigue in TMT bars, several measures can be implemented during both the design and construction phases. Below are some of the most effective strategies for reducing the risk of corrosion fatigue in reinforced concrete structures:
Using corrosion-resistant TMT bars
One of the most effective ways to mitigate corrosion fatigue is by using corrosion-resistant TMT bars, such as those with epoxy coatings or galvanised TMT bars or steels containing corrosion resistant alloying elements such as Cr, Mo, Ni and Cu in correct proportions. These coatings provide a protective barrier that prevents moisture and corrosive agents from reaching the steel surface. Alloying elements like Cr can form a protective oxide layer on the surface whereas elements like Mo, Cu or Ni act as corrosion inhibitors. In addition, newer technologies like the application of corrosion inhibitors directly to the steel surface during manufacturing can significantly reduce corrosion risk.
Improving concrete quality
High-quality concrete is essential for protecting TMT bars from environmental elements. Using a low water-cement ratio and adding supplementary cementitious materials like fly ash or silica fume can reduce the permeability of the concrete, thereby limiting the ingress of water, chlorides, and other harmful substances. Proper curing techniques and the use of high-quality aggregates further contribute to the durability of the concrete, enhancing the protection of TMT bars.
Buy online
Mild SteelStainless SteelStructural SteelTMTCementJSW One MSME
About usBlogsSitemapJSW One TMTPolicy
Terms & conditionsPrivacy policyReturn policyBanking partner