Autoclaved Aerated Concrete (AAC) blocks have emerged as a revolutionary building material in the construction industry. These lightweight and versatile blocks offer a range of benefits, influencing the way walls and partitions are built. Let's delve into autoclaved aerated concrete, exploring its composition, manufacturing process, and the advantages that make it a preferred choice in contemporary construction.
Composition of AAC blocks
AAC blocks are primarily composed of fly ash, cement, lime, gypsum and aluminium powder. What distinguishes them is the inclusion of aeration agents, typically finely powdered aluminium. Aluminium powder is a commonly used gassing agent in AAC production. The pores of AAC are mainly produced by the chemical reaction of aluminium powder in an alkaline environment. The gas forms bubbles under the action of pressure to expand the slurry. The pores produced affect the performance of AAC. This unique blend undergoes a specialised manufacturing process, resulting in a lightweight yet high compressive strength building material.
Cement: Ordinary Portland Cement serves as the binding agent in AAC blocks. It plays a crucial role in holding the other components together, ensuring the structural stability of the blocks.
Lime: Lime is added to improve the workability of the mixture and contributes to the overall durability of the blocks. It reacts with aluminium powder during the curing process, forming hydrogen gas and creating air pockets that give AAC its lightweight nature.
What is an Autoclaved Aerated Concrete (AAC) block?
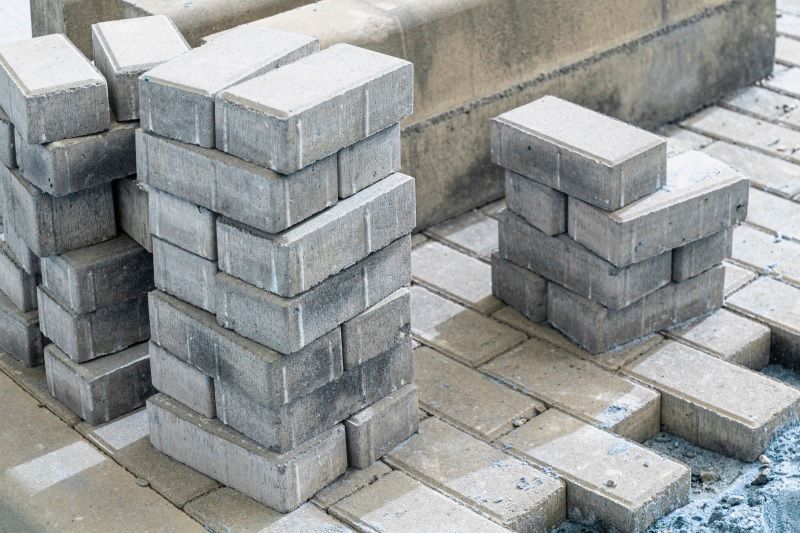
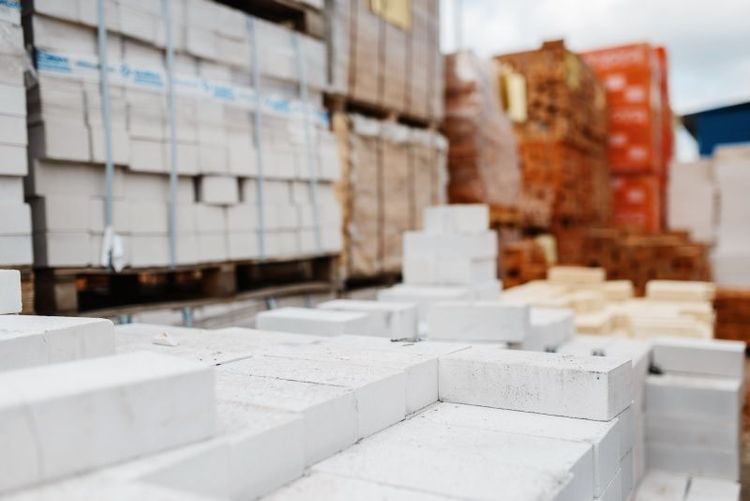
Aluminium powder: The inclusion of finely powdered aluminium is a key factor in the aeration process. When mixed with lime and cement, it reacts with the alkaline elements to produce hydrogen gas, leading to the formation of numerous tiny air bubbles within the mixture.
Manufacturing process
The production of AAC blocks involves a meticulous process that combines science and technology to achieve the desired properties. The key stages in manufacturing include:
Mixing of raw materials: Fly ash, cement, lime, and aluminium powder are mixed in precise proportions to form a homogenous mixture. This mixture is then poured into moulds. The lightweight and insulating properties of the AAC block are due to its expansion and the size of the bubbles, which are typically 2-5mm. After the rising process, the cake is left to settle and pre-cure for 60-240 minutes.
Curing: An autoclave is a 30 to 40-metre-long steel tube with a 3-metre diameter. It is fed with steam at high pressure for 12 hours, typically reaching 800-1200 KPa and a temperature of 180°C. Once the moulds are filled, the curing process begins. This involves exposing the mixture to high-pressure steam, triggering a chemical reaction known as hydration. The reaction causes the lime to react with aluminium powder, releasing hydrogen gas, and forming the characteristic air bubbles.
Cutting and shaping: After curing, the soft blocks are cut into specific dimensions. The cutting process is crucial as it determines the final size and shape of the AAC blocks.
Advantages of AAC blocks
Lightweight: one of the standout features of AAC blocks is their lightweight nature. This characteristic simplifies transportation, reduces construction time, and eases the overall load on the structure.
Thermal insulation: AAC blocks possess excellent thermal insulation properties which are 30% better than bricks, helping to maintain comfortable indoor temperatures. This contributes to energy efficiency and reduces the reliance on artificial heating and cooling systems.
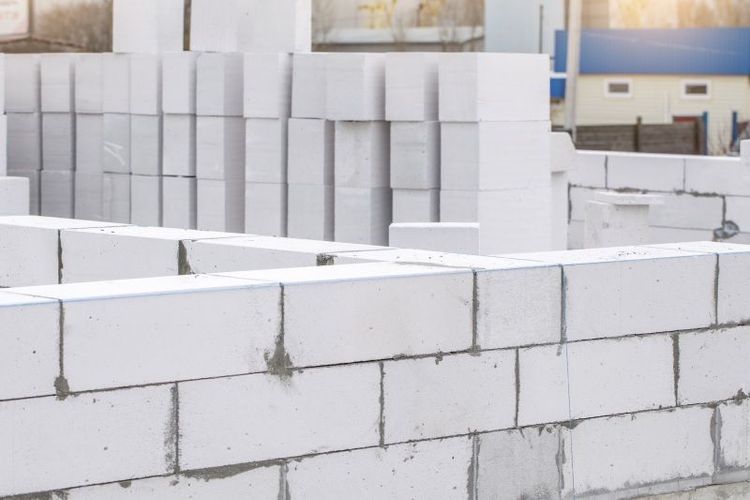
Sound insulation: The porous structure of AAC blocks contributes to effective sound insulation. This is particularly advantageous in urban areas, reducing the impact of external noise and enhancing the overall livability of spaces.
Environmentally friendly: The manufacturing process of AAC blocks involves minimal waste. Additionally, their lightweight nature reduces the carbon footprint associated with transportation.
Durability: AAC blocks exhibit high compressive strength and durability. They resist deterioration caused by environmental factors, ensuring a longer lifespan for walls and partitions built with this material.
Buy online
Mild SteelStainless SteelStructural SteelTMTCementJSW One MSME
About usBlogsSitemapJSW One TMTPolicy
Terms & conditionsPrivacy policyReturn policyBanking partner