The construction industry is a complex ecosystem where every project's success hinges on the seamless flow of materials, equipment, and skilled labour. However, in recent times, the industry has been grappling with a significant challenge: supply chain disruptions. These disruptions, often caused by a myriad of factors such as natural disasters, global pandemics, trade disputes, and transportation issues, have led to delays, increased costs, and logistical nightmares for construction projects worldwide.
Understanding the causes:
One of the primary causes of supply chain disruptions in construction is the global interconnectedness of the industry. Materials sourced from one corner of the world might face delays due to unforeseen circumstances, impacting timelines on a construction site thousands of miles away. For instance, a factory shutdown in one country can lead to a shortage of crucial construction components, causing a ripple effect across multiple projects.
Navigating supply chain disruptions in construction
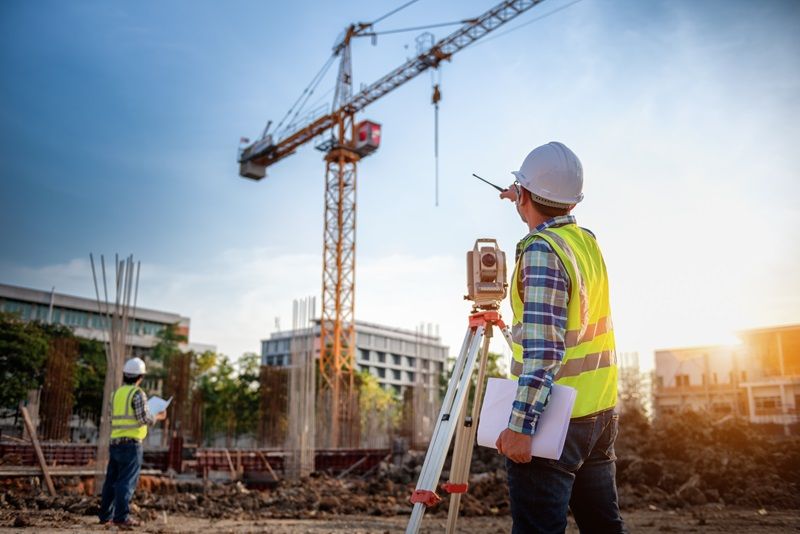
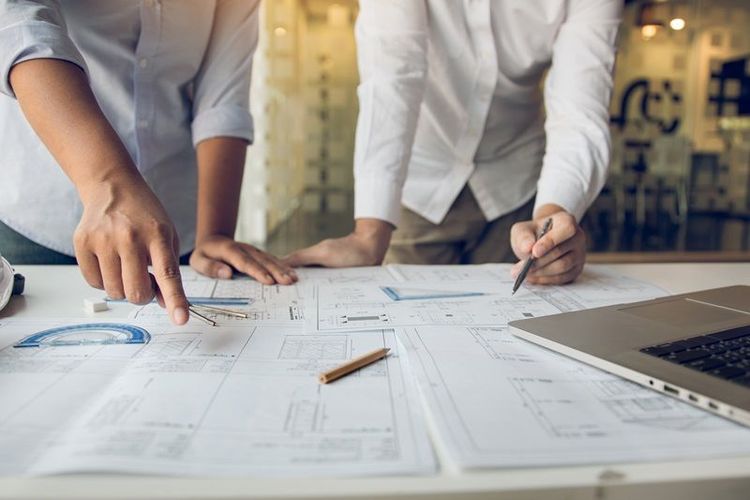
Impact of disruptions on construction projects
Delays, increased costs, penalties:
Supply chain disruptions directly translate into project delays, causing a domino effect on construction schedules. Missed timelines lead to additional costs due to extended labour, overheads, and potential penalties for late delivery.
Increased costs arise from expedited shipping, sourcing alternative materials at higher prices, or paying overtime to mitigate delays, impacting the project's budget significantly.
Effects on project quality and timeline:
Material scarcity may force substitutions, affecting the intended design and compromising quality standards.
Time-sensitive phases of construction might be affected, leading to cascading delays in subsequent project stages, further elongating the overall timeline.
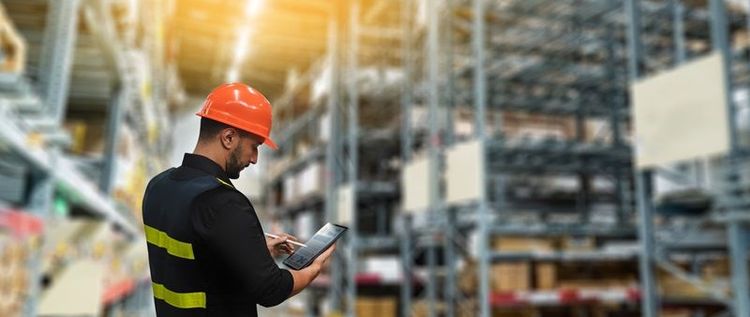
Navigating through disruptions:
While supply chain disruptions can seem insurmountable, proactive measures can help construction companies navigate these challenges more effectively:
- Diversification of suppliers: Relying on a single supplier for critical materials is risky. Diversifying sources can mitigate risks associated with disruptions from a specific region or supplier.
- Communication and collaboration: Maintaining open lines of communication with suppliers, contractors, and stakeholders is crucial. Being aware of potential issues in advance allows for better planning and adaptation.
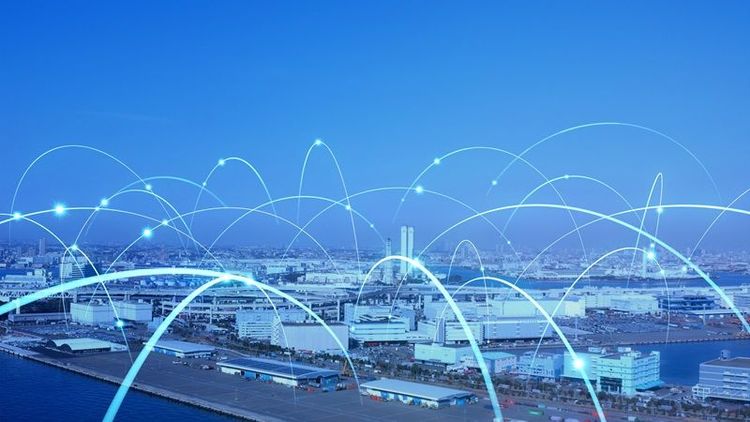
- Technology integration: Embrace technology to track and manage the supply chain. Utilising software for real-time tracking of shipments and inventory levels can provide insights to anticipate and mitigate disruptions.
- Contingency planning: Developing contingency plans for potential disruptions can be invaluable. Having backup suppliers or alternative materials identified in advance can help minimise delays.
- Adaptability and flexibility: Being flexible with project timelines, where possible, and adapting to changes in the availability of materials is key. This might involve redesigning certain aspects or adjusting construction schedules.
- Risk assessment and mitigation: Regularly assess potential risks in the supply chain and develop strategies to mitigate these risks. This proactive approach can help in better preparedness for unforeseen events.
Understanding these causes and impacts is foundational in devising proactive strategies to manage disruptions effectively. Construction companies can implement contingency plans, diversify their suppliers, and leverage technology to track and adapt to changes in the supply chain. Collaboration, adaptability, and a forward-thinking approach are key to mitigating the effects of supply chain disruptions and ensuring project success despite these challenges.
Buy online
Mild SteelStainless SteelStructural SteelTMTCementJSW One MSME
About usBlogsSitemapJSW One TMTPolicy
Terms & conditionsPrivacy policyReturn policyBanking partner