Heat treatments on steel are processes in which steel is subjected to controlled heating and cooling cycles to alter its microstructure and, consequently, its mechanical properties. Different heat treatments can have various impacts on the steel, allowing engineers and metallurgists to tailor its properties for specific applications.
Heat treatment is a crucial process involving controlled heating and cooling of steel to alter its physical and mechanical properties without changing the product shape. This process is particularly significant for hot rolled and cold rolled steel, where it can enhance strength, ductility, durability, and other desired characteristics.
Heat treatment objectives
The primary objectives of heat treatment include hardening, softening and modifying the properties of the steel to achieve desired outcomes such as improved machinability, formability, ductility, and grain size recovery.
Hardening heat treatments
Direct hardening: This involves heating steel to the austenitising range (850 to 950 degrees celsius), followed by quenching (rapid cooling) and tempering at a desired temperature below austenitizing temperature.
Direct hardening increases strength and wear resistance but can decrease toughness meaning the steel doesn’t quite withstand impact. Tempering of directly hardened steel restore ductility and toughness while maintaining strength.
Heat treatments and their impact on steel
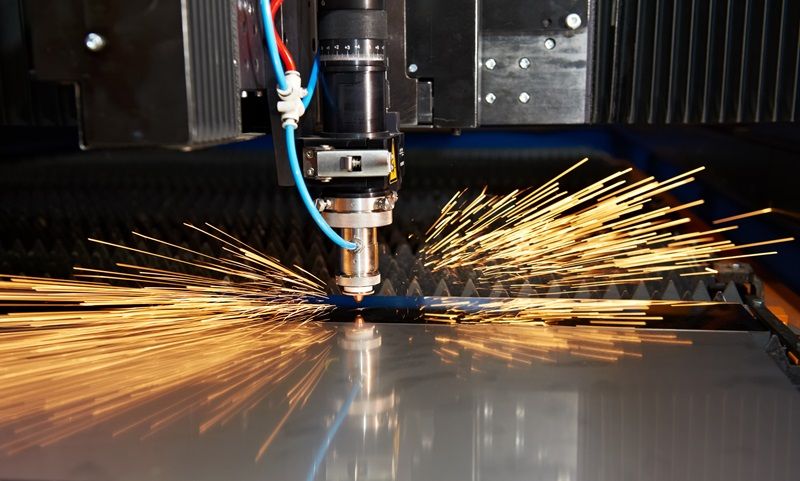
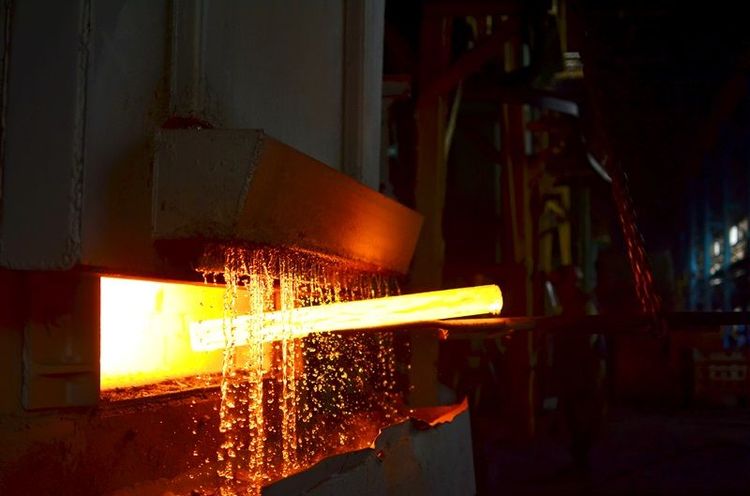
Austempering: A specialised quenching technique where steel is quenched around 315 degrees celsius, above the Martensite Start (Ms) temperature, and held to undergo isothermal transformation to bainite, offering a balance of toughness and hardness. Ms varies according to the carbon and alloy content of the steel.
Austempered steel has high impact strength and a low wear rate meaning there is less material loss over time due to a mechanical action.
Martempering: Similar to austempering but involves further quenching to Ms through Martensite finish (Mf) temperature, resulting in a martensitic structure.
Due to the quenching process, martensite formation results in minimal residual stress. Hence the Martempered steel is dimensionally stable and warps less. Additionally, its parts will have lower distortion (expansion and contraction).
Case hardening: Used for both low and medium/high carbon steels, the process creates a hard, wear-resistant surface and a tough, impact-resistant core.
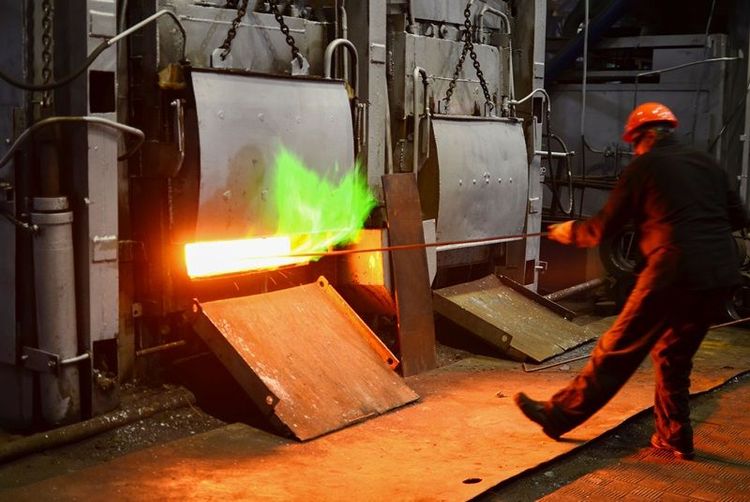
Softening heat treatments
Full annealing: Heating to the austenitising range followed by slow cooling. This process is ideal for hyper-eutectoid steels (0.8% to 2.1% carbon content) and those with coarse grains due to high-temperature hot working.
Full annealing reduces internal stresses and refines grain structure, making the material more pliable for further processing.
Normalising: Heating above the critical temperature into the austenite range, then air cooling at room temperature. This refines the grain structure, improving mechanical properties like strength and toughness while reducing internal stresses.
Process annealing: Used for work-hardened low-carbon steels, it involves heating near the lower critical temperature, followed by cooling.
This reduces internal stresses and improves ductility. This creates a good piece for rolling, drawing, forging and extruding.
Spheroidisation: Suitable for high-carbon steels, this process involves heating just below the eutectoid temperature for extended periods, leading to the formation of spherical cementite particles.
Spheroidisation improves the machinability and formability of the steel by transforming the microstructure into spheroidised carbide particles embedded in a soft ferrite matrix..
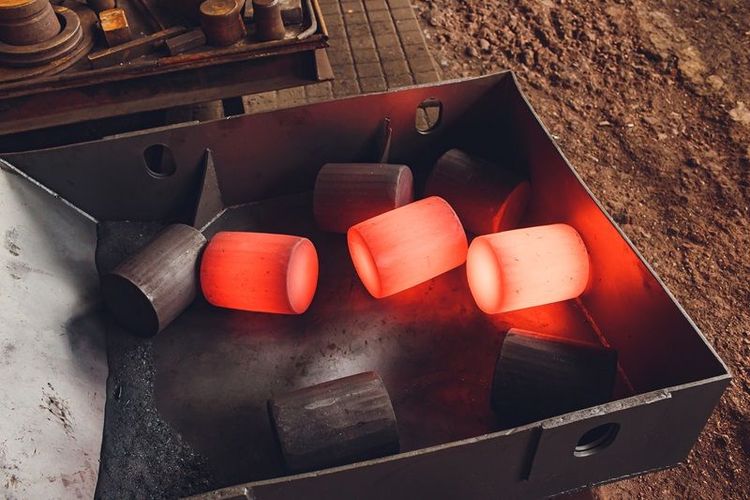
Induction and flame hardening: Localised surface heating by oxy-acetylene or oxy-propane flame (known for their high temperatures) or induction current, followed by quenching. This is used for medium and high-carbon or alloy steels.
Induction hardening is commonly used for selective hardening of toothed surfaces, gears, shafts, and bearing races.
Flame hardening is often used for large components such as axles, crankshafts, and certain machine parts.
Conclusion
Heat treatment techniques for hot rolled and cold rolled steels are diverse and tailored to specific requirements. The selection of a particular method depends on the desired mechanical properties, the steel's composition, and the final application. By leveraging these techniques, one can significantly enhance the performance and longevity of steel products.
Buy online
Mild SteelStainless SteelStructural SteelTMTCementJSW One MSME
About usBlogsSitemapJSW One TMTPolicy
Terms & conditionsPrivacy policyReturn policyBanking partner