Galvanised plain sheets are flat, steel sheets that have been treated with a layer of zinc through a process known as galvanisation. Galvanisation involves immersing the steel sheets in a bath of molten zinc, allowing the zinc to bond to the surface of the steel. As the zinc coating solidifies, it forms a protective barrier, creating a resilient and corrosion-resistant layer over the steel. This coating is what differentiates galvanised plain sheets from their non-galvanised counterparts, making them ideal for withstanding the harsh conditions to which vehicles are exposed.
Benefits of galvanised sheets
The galvanisation process imparts several key advantages to plain steel sheets, making them a preferred choice for automotive manufacturers:
Corrosion resistance: The zinc coating acts as a sacrificial anode, corroding in place of the underlying steel. This protective layer ensures that the sheets remain rust-free even when exposed to moisture, salt, and other corrosive elements on the road.
Strength and durability: Galvanised sheets are significantly stronger and more durable than untreated steel sheets. This strength is essential for various automotive applications, including body panels, chassis components, and structural parts, where durability is crucial for passenger safety.
Galvanised plain sheets in automotive manufacturing
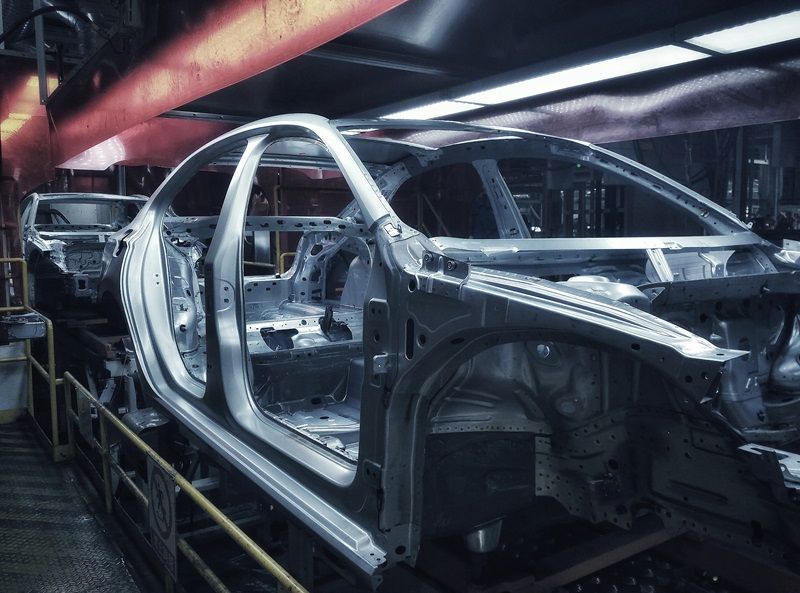
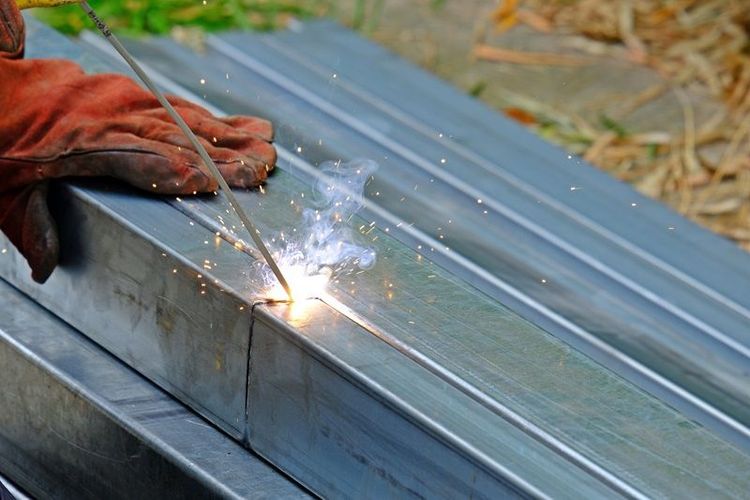
Aesthetic appeal: The smooth and visually appealing finish of galvanised plain sheets enhances their aesthetic appeal, making them suitable for exterior applications and parts visible to consumers. The shiny and uniform surface adds a touch of sophistication to vehicle design.
Cost-effectiveness: While galvanised plain sheets may have a slightly higher initial cost due to the galvanisation process, their extended lifespan and reduced maintenance requirements contribute to long-term cost savings. The reduced need for paint and corrosion protection measures further adds to their cost-effectiveness.
Applications of galvanised plain sheets in automotive manufacturing
Body panels: Galvanised plain sheets are commonly used for manufacturing vehicle body panels such as the roof, doors, fenders, and trunk lids. The galvanised coating provides excellent rust resistance, ensuring the longevity and durability of these components. This is especially important given the exposure to various environmental factors that vehicles endure.
Chassis and frame components: In the construction of a vehicle's chassis and frame, galvanised sheets are often used to enhance strength and longevity. These sheets are known for their high tensile strength and can withstand the stresses and strains experienced by the frame, helping maintain the structural integrity of the vehicle over its lifespan.
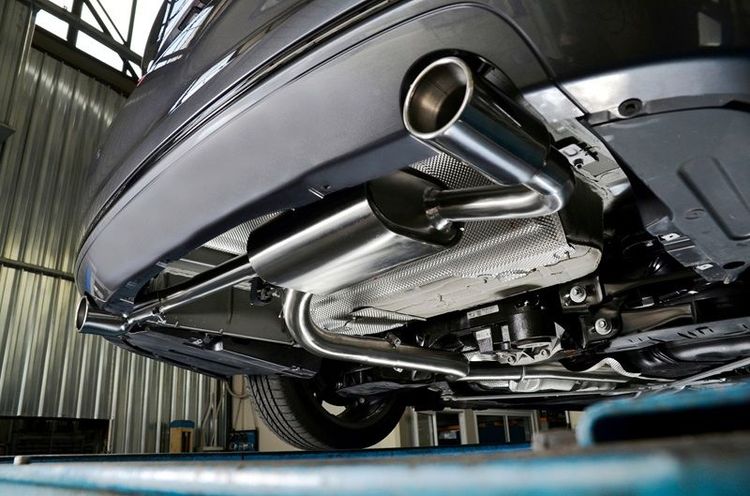
Exhaust systems: Galvanised sheets are used in the manufacturing of exhaust systems, where they are valued for their corrosion resistance. The high-temperature resistance of galvanised coatings ensures that the exhaust system can withstand the heat generated during the combustion process without deteriorating.
Underbody protection: The underbody of a vehicle is exposed to moisture, road salts, and other corrosive elements. Galvanised plain sheets are used to create protective shields for the undercarriage, helping to prevent rust and extend the life of the vehicle.
Interior components: While the exterior components often receive more attention, galvanised sheets also find use in various interior components, such as door panels and seat frames. The corrosion-resistant properties help maintain the aesthetics and structural integrity of these parts.
Safety features: In the interest of passenger safety, automakers use galvanised plain sheets in the manufacturing of safety features such as side impact beams. These beams are vital for absorbing and redirecting impact energy during collisions, and the strength of galvanised steel is a key factor in their effectiveness.
Weight reduction: Automotive manufacturers are continually striving to reduce the weight of vehicles to improve fuel efficiency. Galvanised plain sheets offer a balance between strength and weight, making them an attractive choice for components that need to be both lightweight and robust.
Manufacturing and forming techniques in automotive galvanised plain sheets
Sheet metal stamping is a widely used method for crafting structural components in automotive bodies, while hydroforming is employed for certain automotive parts. Hydroforming shapes metal parts using high-pressure fluid to create intricate and durable components. Roll forming, on the other hand, offers an attractive alternative due to its cost-effective nature for high-volume production and its remarkable flexibility.
Roll forming and stamping
Roll forming:
Roll forming is a widely used manufacturing process in the automotive industry for shaping galvanised plain sheets into complex and continuous profiles. In this technique, the sheets are passed through a series of rollers, each designed to gradually bend and shape the material. The advantage of roll forming lies in its ability to produce long, uniform parts with consistent dimensions. This makes it suitable for producing components like chassis rails, roof rails, and structural reinforcements.
Stamping:
Stamping involves using dies to cut and shape galvanised sheets into precise, complex shapes with high repeatability. It is particularly useful for producing automotive body panels, brackets, and other intricate parts. Stamping can be performed in progressive or transfer presses, with the choice depending on the complexity of the part and the required production volume. The strength and ductility of galvanised plain sheets make them well-suited for stamping processes.
Welding and joining methods
Spot welding:
Spot welding is a common technique used to join galvanised plain sheets in automotive manufacturing. It involves applying localised heat and pressure to melt and fuse the sheets together at specific points. This method is fast, cost-effective, and provides strong and durable joints. It is often employed for joining structural components, such as frame assemblies and chassis parts.
Seam welding:
Seam welding is used to create continuous welds along the length of two galvanised sheets. This method ensures a hermetically sealed joint, making it ideal for applications that require water and air-tight seals, such as fuel tanks and exhaust systems.
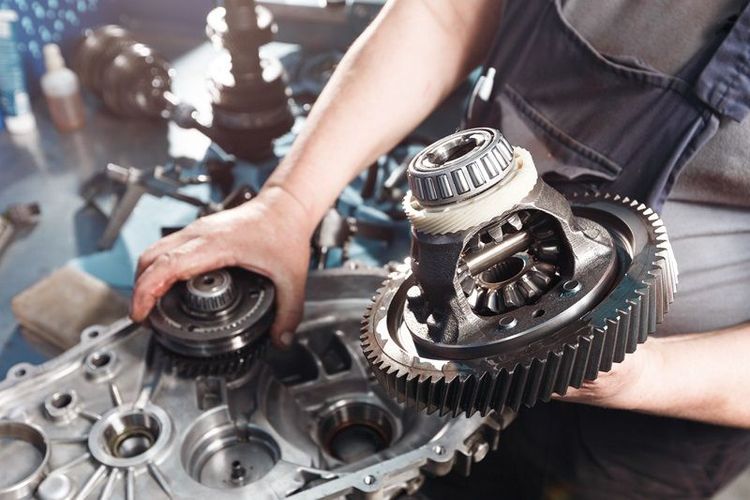
Adhesive bonding:
In addition to welding, adhesive bonding is sometimes used to join galvanised sheets. Adhesives provide an alternative means of securing components and offer advantages in terms of vibration damping and corrosion resistance. This method is often employed in the assembly of automotive interior and exterior trim components.
Buy online
Mild SteelStainless SteelStructural SteelTMTCementJSW One MSME
About usBlogsSitemapJSW One TMTPolicy
Terms & conditionsPrivacy policyReturn policyBanking partner